Latest Articles
Electrical corrosion protection – Prevent hydrogen sulphide corrosion in electrical and electronic equipment
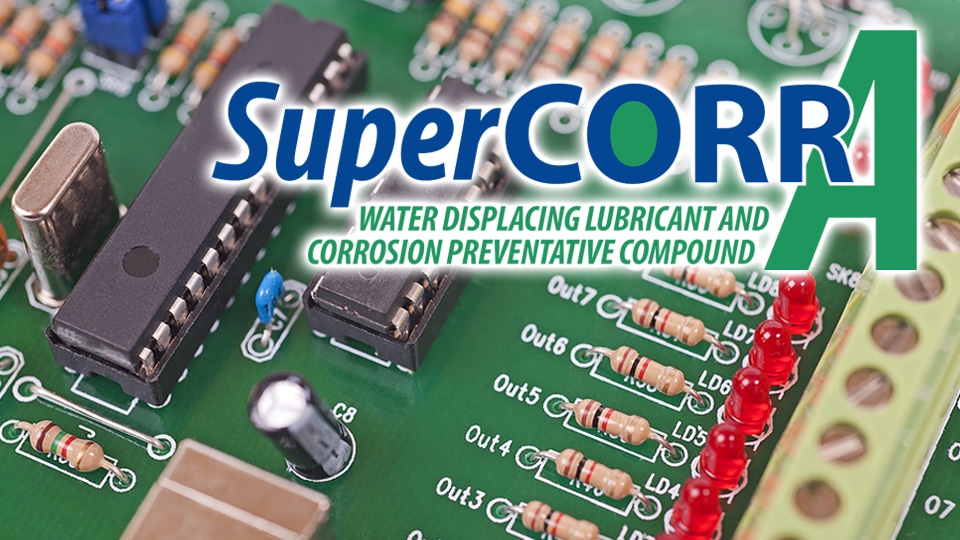
Electrical corrosion protection - Prevent hydrogen sulphide corrosion in electrical and electronic equipment
Corrosion in its many forms, costs both private and public sectors hundreds of billions a year to repair or replace electrical, electronics, or avionic components because of failures caused by corrosion. Lost productivity and revenue caused by plant and equipment corrosion is a serious matter. While all metals corrode, due to a number of different factors, there is no simple or single solution to the overall corrosion problem. However there are some very cost effective and proven ways to prevent corrosion and failures caused by corrosion and thereby reducing or eliminating associated costs and increasing safety which should be foremost in the mind set of any preventative maintenance programme.
Electrical and electronic equipment and components that are used in adverse environments, e.g. the oil and gas industry, waste-water treatment plants and the pulp and paper industry, where corrosive gases such as hydrogen sulphide can be found, cause severe corrosion and the rapid deterioration of the electronic components and equipment including connectors and switches used in these and other work environments. Preventing hydrogen sulphide (H2S) corrosion in electrical and electronic equipment involves a combination of preventive measures and material selection. Here are some steps to mitigate H2S corrosion:
Protective Coatings:
An essential corrosion preventative measure is to apply coatings to vulnerable components. One such coating is Super CORR A advanced lubricant and corrosion inhibiting compound. It will help prevent H2S corrosion in electrical and electronic equipment, ensuring their longevity and reliability in environments where H2S exposure is a concern.
Material Selection:
Choose materials that are resistant to H2S corrosion. For example, stainless steel, nickel alloys, and certain plastics are less susceptible to corrosion by H2S compared to carbon steel.
Enclosures, Sealing and Ventilation:
Seal electrical and electronic equipment and cables in airtight enclosures to prevent H2S exposure. Ensure these enclosures are made from corrosion-resistant materials. Implement ventilation systems to reduce the concentration of H2S in the equipment’s environment.
Monitoring and maintenance::
Regularly monitor H2S levels in the environment where the equipment is installed. Install gas detectors to provide early warnings of increased H2S concentrations. Perform regular maintenance checks on equipment to detect any signs of corrosion. Replace any corroded components promptly.
Design Considerations:
Consider the design of the equipment and its surroundings to minimize the likelihood of H2S exposure. For example, elevating equipment above potential H2S sources can reduce corrosion risk.
Education and Training:
Provide education and training to personnel working with the equipment on the risks of H2S corrosion and the importance of preventive measures.
Emergency Response Plan:
Develop an emergency response plan in case of H2S exposure or equipment failure due to corrosion. This plan should include procedures for evacuating personnel and shutting down equipment safely.
SuperCORR A Specialist Barrier Film Corrosion Protection
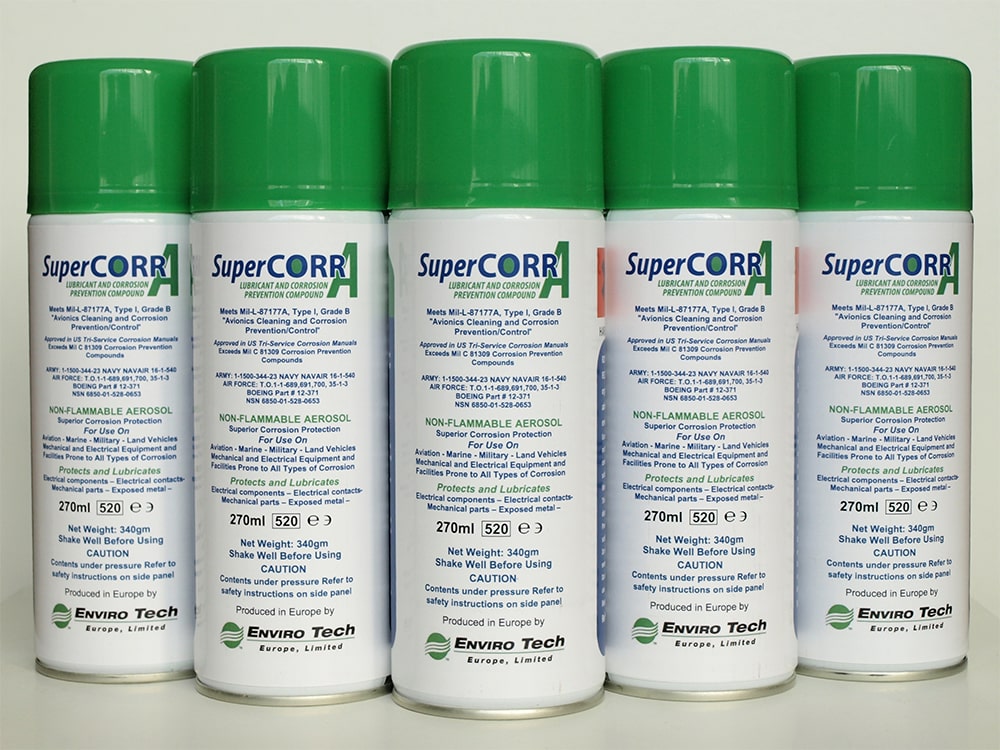
EnviroTech Europe supplies advanced corrosion protection products, based on approved synthetic materials, to provide quality solutions to a diverse range of lubrication and corrosion problems.
Super CORR A is a unique and proprietary formulation with long-lasting, anti-corrosion inhibitors providing a superior lubrication coefficient and protection against moisture, wear, general and fretting corrosion, static electricity, corona, and other electro migration problems. The non-flammable film is only 7 microns (0.007mm) in thickness, is not a wax or oil-based product and is formulated without sulphates, chlorides, petroleum-based material, or halogens, to meet the EU RoHS directive.
The use of Super CORR A for corrosion protection can not only bring financial savings in reduced maintenance and replacement costs but more importantly greater safety. It is much simpler and a lot less costly to prevent corrosion than to repair or replace the damaged equipment or component that failed because of corrosion.
Super CORR A is a proven and cost-effective way to prevent or inhibit corrosion from destroying electronics and electrical components. It was specifically designed to lubricate and prevent corrosion in electrical fittings and connectors; electrical and avionic harness assemblies and connectors; electrical and electronic switches; close tolerance and dissimilar metal components; lighting connectors and sockets. A unique non-flammable “self-healing” ultra-thin film lubricant with a proprietary corrosion preventive compound that will not harden or crack, is not a wax or oil-based product and is formulated without sulphates, chlorides or halogens.
Super CORR A also inhibits corrosion caused by exposure to both fresh and salt water moisture as well as the corrosive vapours from Sulphur dioxide (SO2), Nitrogen dioxide (NO2), Hydrogen Sulphide (H2S), Ammonia (NH3), and Chlorine (CL12) based gases found in waste water and sewer treatment plants, pulp and paper mills and plants, chemical and petroleum plants, maritime industry, aircraft/airline industry, military equipment including ships, aircraft, and rolling stock, auto industry, farming and agriculture industry, and the list goes on.
Super CORR A is packaged in aerosol cans making application to component parts easy for engineering crews in difficult locations and conditions. Unpainted mild steel will not rust on exterior surfaces directly exposed to sea water environments for at least 6 months, protecting electrical connectors, switches, chains, drive shafts from corrosion while maintaining lubrication on moving surfaces.
EFFICIENT AND ECONOMICAL
- Extremely long-lasting, specially formulated and proprietary anti-corrosive inhibitor.
- Eliminates premature failure of components created by moisture, general or fretting corrosion.
- Prevents deterioration and contamination on all surfaces of electronic and electrical equipment and mechanical close tolerance moving components.
- Reliability increased, maintenance intervals increased and costs reduced, manufacturers save costly warranty service calls or product re-call.
HISTORY
Super CORR A was originally developed for the U.S. Air Force to comply with military specifications and to prevent electrical and electronic components from systems failures caused by corrosion. It became the industry standard for avionic corrosion protection within MROs (maintenance, repair and operations) and OEMs (overhaul and original equipment manufacturers). It’s unique ability to displace water and provide a performance enhancing level of corrosion protection has led to it being used in many other applications and industries worldwide.
FURTHER INFORMATION
Please visit our website https://www.envirotech-europe.com/supercorr-a for for information about other uses and applications for Super CORR A.
Visit www.envirotech-europe.com/applications-and-case-studies for information about uses and applications for all EnviroTech Europe products.
For more advice, please telephone us on +44 (0) 20 8281 6370 or use our website contact form. All products are supplied and supported by EnviroTech Europe Ltd. Manufactured in the United Kingdom and available on short delivery times through our dedicated team of distributors worldwide.
Share this page:
Replacements for 3M™ Novec™ Solvents from EnviroTech Europe
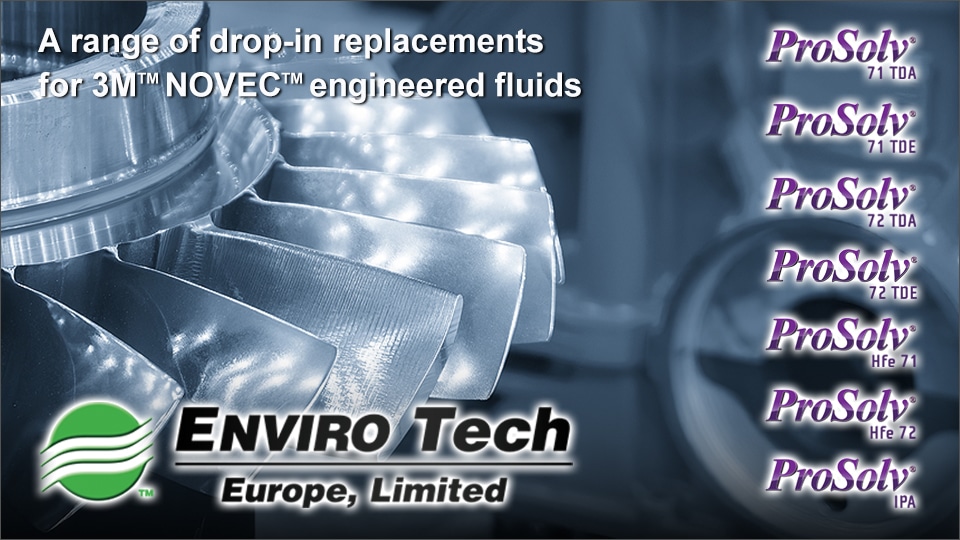
A range of drop-in replacements for 3M™ Novec™ solvents
In December 2022, 3M™ announced their plans to stop producing per- and polyfluoroalkyl substances (PFAS) in its product line by the end of 2025. This phase-out affects the following 3M™ product lines:
3M™ Novec™ Engineered Fluids
3M™ Fluorinert™ Electronic Liquids
ARE YOU AFFECTED BY THE PHASE-OUT OF 3M™ NOVEC™ ENGINEERED FLUIDS?
At Envirotech Europe we can offer replacements with our ProSolv® range for all 3M™ Novec™ solvent cleaning fluids. We understand the uniqueness of every precision cleaning application and provide free on-site visits, technical support and cleaning trials when required.
We can provide a full assessment of your current precision cleaning process to put in a plan to help ensure a seamless transition.
Future-proof your cleaning process with our new ProSolv® range additions.
We have added several cost effective and efficient precision cleaning process formulations to our range of ProSolv® vapour degreasing solvents, offering an immediate drop in replacements for the 3M™ Novec™ engineered fluids.
Introducing ProSolv®5408e, a next generation PFAS free fluorinated solvent offering low GWP and zero ODP.
ProSolv® 5408e is a next generation PFAS free fluorinated solvent offering low Global Warming Potential (GWP) & zero Ozone Depletion Potential (ODP). A general multi-purpose vapour degreasing cleaning solvent that can act as an immediate drop-in replacement for most of the 3M™ Novec™ engineering fluids. We can also deliver an exact formulation replacement of your current solvent should that be your requirements.
EnviroTech Europe have many years of experience and our experts are available to guide you through your solvent cleaner changeover procedures or to advise on equipment. We have extensive partnerships with equipment manufacturers through our global distributors and can provide information and advice on solvents and solvent systems.
FURTHER INFORMATION
Please visit our website https://www.envirotech-europe.com/prosolv5408e for information about other uses and applications for ProSolv® 5408e.
Visit www.envirotech-europe.com/applications-and-case-studies for information about uses and applications for all EnviroTech Europe products.
For more advice, please telephone us on +44 (0) 20 8281 6370 or use our website contact form. All products are supplied and supported by EnviroTech Europe Ltd. Manufactured in the United Kingdom and available on short delivery times through our dedicated team of distributors worldwide.
Share this page:
Related Posts
The importance of corrosion protection for electric vehicles
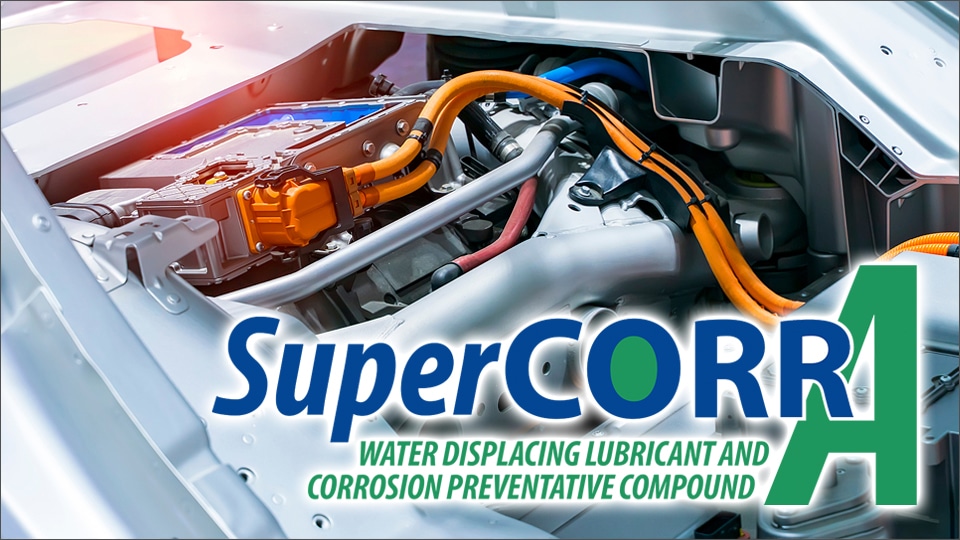
The importance of corrosion protection for electric vehicles
Corrosion protection is as important for electronic vehicles (EVs) as it is in traditional petrol/gasoline powered vehicles. However, there are some unique factors to consider when it comes to avoiding corrosion problems in electric vehicles:
Battery Enclosure and Connections:
EVs have large, heavy battery packs that are typically enclosed in a protective housing. This enclosure and its connections can be particularly susceptible to corrosion, especially in regions with high humidity or exposure to road salt. Corrosion in the battery enclosure or on electrical connections can affect the performance and safety of the vehicle.
Charging Infrastructure:
Charging equipment, especially in public charging stations, can be exposed to the elements. The connectors, plugs, and wiring can corrode over time. This can lead to issues with charging reliability and safety concerns.
Cooling Systems:
Many EVs use liquid cooling systems to manage the temperature of the battery. The components in these systems, such as radiators and coolant lines, are vulnerable to corrosion. The resulting leaks or blockages in the cooling system can potentially lead to overheating and reduced battery life.
Underbody and Frame:
Just like traditional vehicles, EVs have underbody components such as the chassis, suspension, and brake components that are susceptible to corrosion, especially if the vehicle is driven in areas where roads are salted during winter. Corrosion can weaken the structural integrity of the vehicle.
Electrical Contacts and Connectors:
Electrical connectors and contacts throughout the vehicle can corrode, leading to issues with sensors, lights, and other electrical systems. This can affect overall performance and safety.
Material Longevity:
EVs often incorporate a variety of materials, including metals and alloys, in their construction. Corrosion can significantly reduce the lifespan of these materials, leading to premature failure of crucial components. Protecting against corrosion ensures the durability and reliability of the vehicle over time.
Safety Concerns:
Corrosion can compromise the structural integrity of a vehicle, posing safety risks for occupants. In an EV, where advanced technologies and high-voltage systems are prevalent, maintaining structural integrity becomes even more critical. Proper corrosion protection helps mitigate these concerns.
Performance and Efficiency:
Corrosion on electrical components, connectors, and conductive elements can hinder the performance and efficiency of an EV. For instance, corrosion on battery terminals may increase electrical resistance, leading to reduced energy transfer efficiency and overall performance. Ensuring corrosion-free connections is vital for maintaining optimal efficiency.
Cost Savings:
Corrosion-related damage can result in expensive repairs and replacements. By investing in effective corrosion protection measures, manufacturers and owners can avoid these costs, contributing to the overall economic viability of electric vehicles.
Environmental Impact:
EVs are often considered more environmentally friendly than traditional vehicles. However, if corrosion leads to premature scrapping of EVs or frequent replacement of components, it can undermine their environmental benefits. Proper corrosion protection helps maintain the longevity of EVs, reducing their overall environmental impact.
Maintaining Resale Value:
Corrosion damage can significantly reduce the resale value of a vehicle. As EVs become more common in the used car market, maintaining corrosion protection becomes essential for preserving the value of these vehicles over time.
Regulatory Compliance:
Different regions have regulations and standards regarding vehicle safety. Corrosion protection is often a requirement to meet these standards and ensure that EVs adhere to guidelines.
Aesthetic Considerations:
Corrosion can also affect the appearance of a vehicle. For EV manufacturers who emphasize design and aesthetics, ensuring that the vehicle maintains its visual appeal over time is crucial for customer satisfaction.
To mitigate and address corrosion issues in EVs, manufacturers take the various measures, including the use of corrosion-resistant materials, applying protective coatings and sealants to prevent moisture and salt exposure, regular maintenance and warranty coverage. It’s important for EV owners to follow manufacturer recommendations for maintenance and care, as well as be aware of their local environmental conditions. Proper care and maintenance can help reduce the risk of corrosion and ensure the longevity and safety of the vehicle. Additionally, addressing corrosion issues promptly can prevent them from becoming more serious and costly problems in the long run.
In summary, implementing corrosion protection measures for electronic vehicles should be based on specific circumstances and environmental conditions. Corrosion protection is fundamental for the long-term performance, safety, and sustainability of electric vehicles. It addresses not only technical and safety considerations but also contributes to the overall economic and environmental viability of EVs in the automotive market.
SuperCORR A Specialist Barrier Film Corrosion Protection
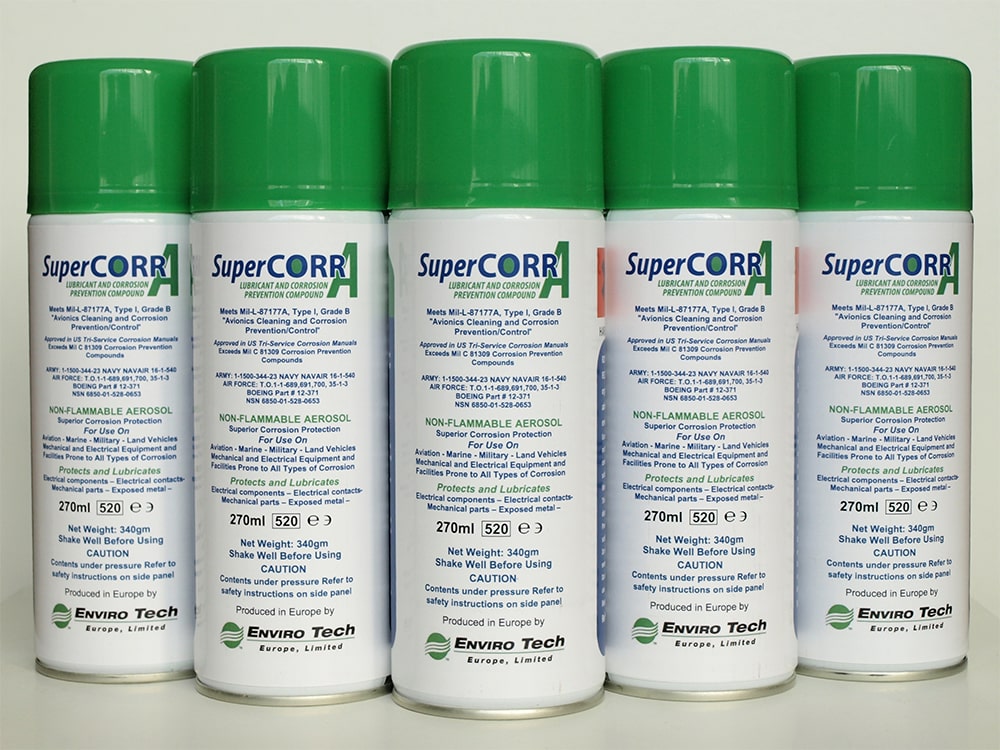
EnviroTech Europe supplies advanced corrosion protection products, based on approved synthetic materials, to provide quality solutions to a diverse range of lubrication and corrosion problems. SuperCORR A is a unique and proprietary formulation with long-lasting, anti-corrosion inhibitors providing a superior lubrication coefficient and protection against moisture, wear, general and fretting corrosion, static electricity, corona, and other electro migration problems. The non-flammable film is only 7 microns (0.007mm) in thickness, is not a wax or oil-based product and is formulated without sulphates, chlorides, petroleum-based material, or halogens, to meet the EU RoHS directive.
SuperCORR A is unexcelled in preventing failures of electrical systems and electronic equipment caused by corrosion as well as preventing the corrosion of metal components surfaces, including those of components comprised of dissimilar metals such as those found in aerospace environments.The ability to displace water from exposed contacts can ensure reliable operation in extreme conditions. The use of SuperCORR A for corrosion control can not only bring financial savings in reduced maintenance and replacement costs but more importantly greater safety. It is much simpler and a lot less costly to prevent corrosion than to repair or replace damaged avionic equipment or a component that failed because of corrosion.
SuperCORR A is packaged in aerosol cans making access to component parts easy for engineering crews in difficult locations and conditions. Unpainted mild steel will not rust on exterior surfaces directly exposed to sea water environments for at least 6 months, protecting electrical connectors, switches, chains, drive shafts from corrosion while maintaining lubrication on moving surfaces.
EFFICIENT AND ECONOMICAL
- Extremely long-lasting, specially formulated and proprietary anti-corrosive inhibitor.
- Eliminates premature failure of components created by moisture, general or fretting corrosion.
- Prevents deterioration and contamination on all surfaces of electronic and electrical equipment and mechanical close tolerance moving components.
- Reliability increased, maintenance intervals increased and costs reduced, manufacturers save costly warranty service calls or product re-call.
HISTORY
SuperCORR A was originally developed for the U.S. Air Force to comply with military specifications and to prevent electrical and electronic components from systems failures caused by corrosion.
It became the industry standard for avionic corrosion protection within MROs (maintenance, repair and operations) and OEMs (overhaul and original equipment manufacturers). It’s unique ability to displace water and provide a performance enhancing level of corrosion protection has led to it being used in many other applications and industries worldwide.
FURTHER INFORMATION
Please visit our website https://www.envirotech-europe.com/supercorr-a for for information about other uses and applications for Super CORR A.
Visit www.envirotech-europe.com/applications-and-case-studies for information about uses and applications for all EnviroTech Europe products.
For more advice, please telephone us on +44 (0) 20 8281 6370 or use our website contact form. All products are supplied and supported by EnviroTech Europe Ltd. Manufactured in the United Kingdom and available on short delivery times through our dedicated team of distributors worldwide.
Share this page:
Latest News
Vapour degreasing – A guide for production engineers
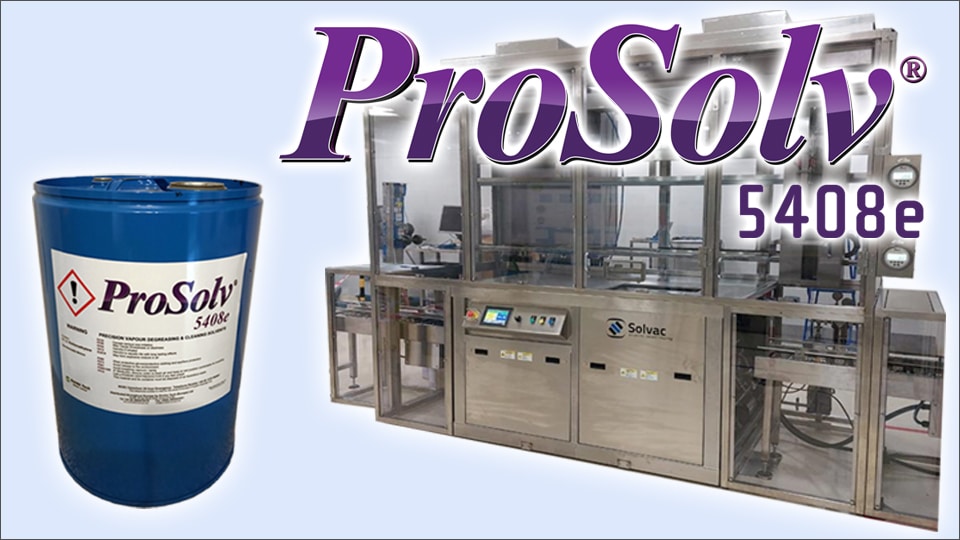
Vapour degreasing – A guide for production engineers
This guide for production engineers explains why vapour degreasing is the most effective and economical process for cleaning of manufactured components. The start of a new year is always a good time to review your existing cleaning process and ask yourself ‘am I using a safe modern solvent for vapour degreasing?’.
Vapour degreasing is the simplest but most effective degreasing and cleaning process which, until recently, has been subject to little change since it was first invented in the early part of the last century. This is a very mature chemical technology which legislation is now effecting changes so fundamental that the more accurate name for the process “Condensation Cleaning” should be used to reflect the improvements in equipment design, chemistry, reduced emissions, economies in usage of solvents and the subsequent environmental acceptability compared to the open topped tanks so ubiquitous in factories and workshops worldwide. The alternatives in equipment design offer differences in technology, which guarantee the continuing use of this process in the future, need to be considered and understood.
The cleaning tank in the corner of most engineering shops hides a very well researched process using sophisticated chemistry. Its popularity is in its simplicity. The tank sump is heated, fitted with cold coils around the internal surfaces at the top to retain the vapour. Fill to a few centimetres with a non-flammable solvent able to dissolve contaminants, boil to form a vapour 3 to 4 times heavier than air to fill the tank. Hot solvent vapour condenses on the cooler target parts at workplace temperature. The hot liquid solvent dissolves oil and grease and other contaminants. Used solvent returned to the sump revaporises continuing the cycle until parts have achieved the same temperature as the vapour when, with no further condensation, the process is complete. Simple but perfect. Highly productive and economical, parts removed from the cleaning process are clean, warm, and dry in 5 to 10 minutes.
Historically chlorinated hydrocarbons have been the solvents of choice for the “Condensation Cleaning” process. Compatible with most materials of manufacture, stable in constant use, producing a non-flammable saturated vapour heavier than air at a temperature greater than ambient. In Europe, the United States and in other advanced industrialised economies increasingly stringent legislation to control emissions of VOCs, especially solvents, has led to new formulations for paints and other coatings where water replaces most of the solvent. In the early days the quality of water-based paints was not as good as traditional solvent-based coatings, but innovation has driven the development of new polymers with results as good as, if not better than, the solvent-based originals.
As with coatings, cleaning systems have had to change. With increasingly demanding standards of cleaning required for precision engineering, electronics, optics etc solvents are often first choice, for reasons outlined above, but these have been targeted by regulators and alternatives are encouraged by the relevant authorities and law makers often without serious consideration of unintended consequences. For example, water-based cleaning is encouraged as the obvious alternative, but this has many disadvantages compared to condensation cleaning as although the machines are simple and relatively cheap the processes require multiple heated tanks for immersion or spray processing or long programmed cycles in batch machines for cleaning, rinsing, and drying. Water based processes are slow, energy intensive and occupy more floor space than solvent-based condensation cleaning equivalents where only one tank with a small footprint is needed, delivering shorter process times and, most importantly for the environment, using minimal energy.
The ideal cleaning process would be “Condensation Cleaning” using water but due to the physical characteristics of the water vapour/steam and the inability to carry onto the surface of the targeted parts surfactants to remove the oil, grease and soils and the difficulty and expense of rinsing and especially drying this can only ever be a dream.
Historically chlorinated hydrocarbons have been the solvents of choice for the “Condensation Cleaning” process. Compatible with most materials of manufacture, stable in constant use, producing a non-flammable saturated vapour three to four heavier than air at a temperature greater than ambient. The traditional solvents such as trichloroethylene exhibits all these characteristics however concerns about its carcinogenic properties and the danger to operators by exposure, led to a continuing search for a safer alternative. 1,1,1 trichloroethane based solvent formulations became popular in the mid part of the last century as a safer replacement. An excellent solvent, safer for users, it proved to be depleting the protective ozone layer around the Earth and was subsequently banned. With the development of the REACH legislation in Europe, trichloroethylene was again allowed with restrictions and stringent controls for use in authorised machines which control emissions to very low figures close to zero.
High performance vapour degreasing and cleaning
EnviroTech Europe have been supplying vapour degreasing solvent formulations for 40 years constantly responding to increasingly stringent regulatory requirements for environmental and safety laws and the need for improved cleaning standards. ProSolv® 5408e is a new sustainable solvent blend with near zero OPD (Ozone Depletion Potential) and GWP (Global Warming Potential) for high performance degreasing and cleaning which ticks all the boxes with the perfect profile for a vapour degreasing solvent. Soft on the environment and safer for users with high performance, improved cleaning, and lower costs. Lower boiling point, economical with energy with low solvent losses, faster production, reduced costs, easy handling. Exceptionally low surface tension to penetrate micron sized holes and close contact surfaces. Sustainable and secure for future use as your ‘forever solvent’.
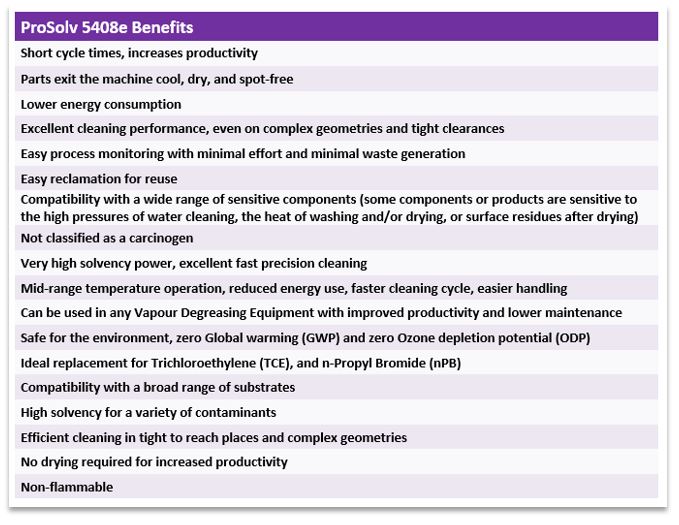
Sealed Tanks
As with all legislation for chemical use regulation and restrictions drive development of associated processes and equipment. Sealed tanks are now standard with many different designs available. The most common are discussed below.
The single tank hermetically sealed machines favoured by some manufacturers uses a process tank to contain the solvent and a separate storage tank/vapour generator. Baskets loaded with parts to be cleaned are introduced from the top or through access points on the side of the tank. Lids or doors hermetically seal the tank. Solvent is pumped into the process tank where agitation, ultrasonics or pumped liquid is circulated through the parts. Used Solvent is removed to the vapour generator, condensing coils controlling the vapour are linked to coils located in the vapour zone which, when the cycle is complete, collapse the vapour. The process tank is emptied. Controlled air introduced to process tank is then recycled through carbon absorption units to remove traces of solvent until the concentration is within regulatory standards when the lid is released for the basket of parts, clean and dry, to be removed and replaced with a further basket. Variations of process within the hermetically sealed tank are possible using sprays of cold or hot condensed solvent, immersion with or without ultrasonics and revolving baskets to cover most of the problems experienced when processing machined and fabricated parts. Continuous external distillation of the contents of the vapour generator is also an option depending on contamination.
The alternative technology is much simpler and uses well tried techniques not requiring the long recovery times of the hermetically vacuum sealed processes. The multilevel system uses a standard vapour degreasing tank design with a sealed loading section above the process tank. Components to be cleaned loaded in work baskets or jigs are fed to the load section by hand or conveyor, an internal platform raises and lowers the baskets in controlled cycles.
Loading complete – the load enclosure is sealed to completely isolate the process. Then seal on the process tank is opened and the basket automatically lowered into the cleaning section which can be simple condensation cleaning or immersion cleaning with or without ultrasonics or power sprays. Revolving baskets can also be added to improve cleaning in blind or through holes or oil ways in castings and fabrications.
On completion the basket rises to the area where the condensation coils are located, and parts allowed to drain and dry, basket raises into the load section when the process tank is sealed. A fan circulates air within the load area which can be recycled through carbon absorption systems if no external exhaust is preferred.
As baskets entering the loading space contain parts drained and dried only very small amounts of solvent are carried in the exhausted air which is monitored to ensure compliance with appropriate legislation. When this is complete the seal opens fully for removal of cleaned components. The loading section can be fitted with top or side seals allowing baskets to flow through on conveyor systems or be removed by hand or hoist. No solvent enters the work area. Both processes will produce parts cleaned to the highest standards but the choice of which offers the best solution needs a little more consideration.
The hermetically sealed vacuum process is complicated with the need to move liquids in the machine. It is relatively slow as the carbon adsorption process has to remove high levels of solvent from the recirculated airstream from the process tank. This is inefficient as adsorption rates for carbon fall rapidly with increasing saturation. Final levels of solvent in the tank when the lid or loading door opens will be dragged into the workshop and the area where the operator is working. Long process cycles reduce throughput.
The simpler multilevel systems where movement of liquids is not required are more efficient and offer much faster process times. Cost of manufacture is also reduced as no liquid movement or vacuum is involved. The extracted loading section ensures no leakage of solvent into the work area giving complete safety for operators and factory staff. Envirotech Europe also offers workplace air monitoring to ensure VOC’s from the solvent are within exposure limits and your machine is operating to specification.
Conclusions
Both designs of process machines discussed above fully comply with the emission regulations of the EU and U.S authorities. Which to choose will depend on many factors which should be discussed with equipment and solvent suppliers who have the experience to advise on which offers the best process for the application. Equipment and solvent must work together, so it is advisable to ensure that the suppliers co-operate to offer a package with high levels of responsible care and product stewardship to ensure the best and safest installation. EnviroTech personnel and distributors are trained to work with equipment suppliers to advise on the use of ProSolv® 5408e vapour degreasing solvent for the most satisfactory outcome.
The “Condensation cleaning” process still gives the highest levels of economical cleaning with minimum energy usage, low footprint on the factory floor, safety for the operator, and high production rates with low solvent usage and environmental impact. With the new generation of sealed cleaning machines its future as the process of choice is assured.
Photograph of Solvac equipment courtesy of C&C Hydrosonics.
FURTHER INFORMATION
Please visit our website https://www.envirotech-europe.com/prosolv5408e for information about other uses and applications for ProSolv 5408e.
Visit www.envirotech-europe.com/applications-and-case-studies for information about uses and applications for all EnviroTech Europe products.
For more advice, please telephone us on +44 (0) 20 8281 6370 or use our website contact form.
All products are supplied and supported by EnviroTech Europe Ltd. Manufactured in the United Kingdom and available on short delivery times through our dedicated team of distributors worldwide.
Share this page:
Related Posts
Video: ProSolv 5408e – Vapour degreasing cycle using hermetically sealed equipment
Vapour degreasing cycle using hermetically sealed equipment.
ProSolv 5408e is a high- performance solvent cleaner used for sustainable and future proof vapour degreasing. Soft on the environment and safe for users, it offers improved cleaning at lower costs. Low boiling point, economical with energy with low solvent losses, faster production.
Innovation driven by legislation
Vapour degreasing, with or with-out ultrasonics, is the oldest, simplest and most effective solvent degreasing and metal cleaning process used today. It has, until recently, been subject to little change since it was first invented in the early part of the last century. In the UK, Europe, United States and other advanced industrialized economies increasingly stringent legislation to control emissions of VOCs, Solvents with a high Global Warming Potential (GWP), or a high Ozone Depletion Potential (ODP), and those compounds associated with human health concerns has led to Envirotech Europe manufacturing new formulations for precision cleaning solvents with low or near zero potential.
Halogenated hydrocarbons are the solvents of choice for vapour degreasing and cleaning. The process is essentially simple. A tank with a sump to contain the solvent, heaters at the base and condensation coils around the top section to control the height of the vapour is all that is needed. When heated in the sump halogenated solvents produce, in most cases, a saturated vapour between 3 and 4 times heavier than air at a temperature greater than the ambient temperature of the parts to be cleaned. This allows the solvent vapour to condense on the surface of the parts. The condensate dissolves the contaminants such as oil, greases, flux, and soils returning the used solvent into the sump of the machine for recycling into vapour which continuously condenses onto the parts until they have achieved vapour temperature when, with no further condensation, the process is complete. Parts removed from the cleaning machines are very clean, warm and dry.
The most common halogenated solvents, in use for commercial purposes, are non-flammable so present no risk in this process. Perchloroethylene, used mainly for dry cleaning, methylene chloride previously used widely in paint strippers, 1,1,1- trichloroethane and trichloroethylene used for vapour degreasing were the original materials used based on chlorine chemistry. However continuing concern about the environmental impact and danger to operators by exposure to chlorine-based solvents, especially trichloroethylene, has led to a continuing search for safer alternatives, such as ProSolv 5408e , a trans-1,2-Dichloroethylene based solvent mixture that is non-flammable.
The ProSolv 5408e vapour degreasing process gives the highest levels of economical cleaning with minimum energy usage, low footprint on the factory floor, safety for the operator, and high production rates with low solvent usage or environmental impact. With the new generation of sealed cleaning machines its future as the process of choice is assured.
A more detailed version of this article can be viewed here:
https://www.vapour-degreasing.com/solvent-degreasing-and-metal-cleaning/
Animation of Solvac hermetically sealed equipment by kind permission of CC Hydrosonics Ltd. https://www.cchydrosonics.com/
FURTHER INFORMATION
For more advice, please telephone us on +44 (0) 20 8281 6370 or use our website contact form. All products are supplied and supported by EnviroTech Europe Ltd. Manufactured in the United Kingdom and available on short delivery times through our dedicated team of distributors worldwide.
Share this page:
The best in vapour degreasing, corrosion protection, metal cleaning and surface treatment
EnviroTech Europe are specialists in metal, plastic and other substrate cleaning, pretreatment and protection.
We offer a range of approved products tailored to your industry, which are cost effective, energy efficient, safe for operators and the environment.
Our products are used in the following industries:
- Electronics and Electrical
- Environmental
- General Cleaning
- Industrial and Manufacturing
- Marine and Maritime
- Mechanical Engineering
- Medical Device Manufacturing
- Military
- Motorsport
- Power Generation
- Railways and Automotive
PRODUCTS:
EnSolv CC-A Vapour Degreasing Solvents For Precision Metal Cleaning:
A family of environmentally friendly precision vapour degreasing and cleaning solvents for the aerospace, precision engineering, medical, optical and electronic industries.
ProSolv 5408e Environmentally Sustainable High Performance Vapour Degreasing Solvent:
Zero ODP (ozone depletion) and GWP (global warming potential) – Sustainable and secure for the future.
SuperCORR A Advanced lubricant and corrosion protection compound:
Specialist barrier film corrosion protection products, based on synthetic materials to provide safe, effective, environmentally friendly solutions to lubrication and corrosion problems.
Aquus CL-One General Purpose Industrial Cleaning Agent:
A non-toxic, water based surfactant system which exhibits a combination of characteristics not found in any comparable commercially available system.
Clarea Industrial Degreasing Solvents:
Non chlorinated, industrial wipe, brush, dip and immersion cleaning solvents for removing dirt, oil, grease and other contaminants without causing harm or leaving residue.
VOC Exposure Monitoring:
We have portable test equipment that logs the Volatile Organic Compound (VOC’s) content in the air from various strategic positions around your degreasing equipment, including the operator position
FURTHER INFORMATION
For more advice, please telephone us on +44 (0) 20 8281 6370 or use our website contact form. All products are supplied and supported by EnviroTech Europe Ltd. Manufactured in the United Kingdom and available on short delivery times through our dedicated team of distributors worldwide.
Share this page:
Industrial solvent cleaners
Clarea® general purpose industrial solvent cleaners are safe for users and the environment
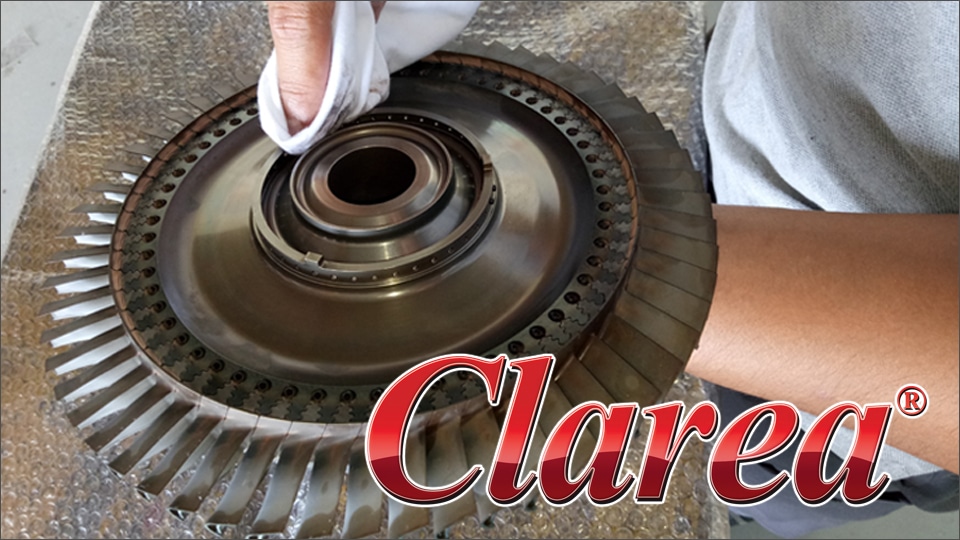
Clarea® non-chlorinated industrial solvent cleaners are compatible with all metals, composites and most plastics used to remove dirt, oil, grease, or other contaminants from surfaces without causing harm or leaving residue. They are used as immersion cleaners for component cleaning in manufacturing and engineering industries and as wipe cleaners for large surface areas prior to painting or powder coating. The environmental concerns and health hazards of the chlorinated solvents used as industrial degreasing agents has led to the formulation of this EnviroTech range of safer cleaning solvents.
What to consider when choosing suitable solvent cleaning products?
Solvents used for cleaning must be highly refined and leave no residues on drying. They need to be highly effective removing oils and soils without causing damage or corrosion of the parts or components being processed and leave minimal residues.
Cleaning specifications vary widely from very demanding automotive and aerospace applications to less demanding applications where critical cleaning is not needed such as pre-used parts or assemblies from the transportation, aerospace, or manufacturing equipment sectors. Heavily contaminated when removed from service these must be free of oils, soils, grease and dirt before disassembly prior to refurbishing and rebuilding. Much of this work will be manual and the considerations for the safety of operators, hand wiping or brush cleaning is paramount.
Clarea® products are aliphatic hydrocarbon based low odour degreasing solvents with specified flash points. They will remove oils, greases, hydraulic fluids cutting fluids and a wide variety of hydrocarbon based protective coatings. Clarea® solvents can be safely used with all metals and composites and most plastic and paint finishes.
Clarea® HC40 is low odour degreasing fast drying solvent with a flash point of 40°C. It is suitable for ultrasonic and dip systems and can be used with brush or in hand-wipe processes.
Clarea® HC462 is a degreasing solvent with a flash point over 60°C. It is suitable for hand-wipe applications when used externally.
EFFICIENT AND ECONOMICAL
- Versatile and cost-effective solutions for all your industrial cleaning
- Minimal odour and low toxicity for operators
- Multipurpose uses can reduce the inventory of cleaning fluids.
- Flexible uses – evaporation rates suitable for hand wipe, spray, or immersion tank cleaning
- Clarea HC40 for brush and hand wiping, air dries. Flash point 40°C
- Clarea HC62 for spray or immersion cleaning Flash point 62°C
- Contains no chlorine, other halogens or stabilisers
- Compatible with all metals and composites and most plastics
- Excellent pre-cleaner for paint or powder coatings
- Safe, reliable, environmentally friendly cleaning
We can provide you with a Material Safety Data Sheets, independent laboratory reports, product samples and technical assistance.
For more information or advice please telephone us on +44 (0) 20 8281 6370 or use our contact form.
All products are supplied and supported by EnviroTech Europe Ltd. Manufactured in the United Kingdom and available on short delivery times through our dedicated team of distributors worldwide.
Share this page:
Related Posts
Solvent Cleaner For Electronics
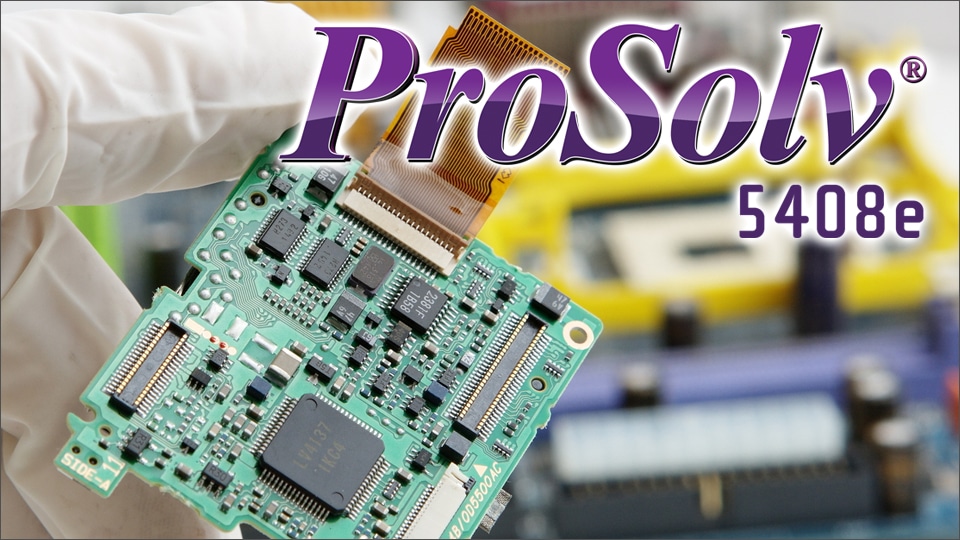
High performance solvent cleaner for electronics and electrical components
Evolving legislation by governments worldwide has resulted in the need for new and original formulations to be offered for use in solvent cleaning and vapour degreasing processes. Companies must continue to comply with legislation for protection of the environment and safety of operators who may be exposed to harmful substances. In applications where formulated blends of halogenated solvents have been used very effectively in the past, these are now required by changes in legislation to be phased out of use.
With a wealth of experience in this field, EnviroTech Europe have developed a new solvent cleaning formulation based on recent research, a replacement for the “old” technology, which has been found to perform just as effectively without the negative environmental, health and safety issues.
Near Zero OPD and GWP solvent blend for high performance vapour degreasing solvent cleaner
ProSolv 5408e is the perfect replacement for trichloroethylene, nPB (n-propyl bromide), perchloroethylene or other flammable solvents used in general engineering cleaning processes.
ProSolv 5408e is a high-performance solvent cleaner used for sustainable and future proof vapour degreasing. Soft on the environment and safe for users, it offers improved cleaning at lower costs. Non-carcinogenic, low boiling point, economical with energy with low solvent losses, faster production, reduced costs, easy handling.
ProSolv 5408e has been developed to provide superior critical cleaning performance for manufacturers of electronic and electrical components. High Solvency (KB Value 98) for removal of organic residues, compatible with organic and synthetic oils and most plastics and metals,
non-flammable, with low ozone depletion (ODP) and global warming potential (GWP).
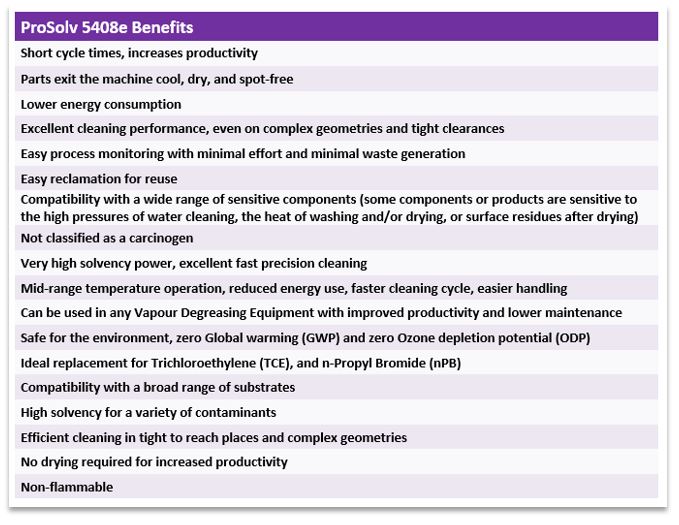
Listed above are some of the benefits from using ProSolv 5408e, a sustainable vapour degreasing solvent for cleaning and defluxing in the electronics and electrical components industry and an economical and efficient replacement solution for vapour / vapour liquid cleaning systems using older legacy solvents, which are now either banned or being phased out. EnviroTech Europe have many years of experience and our experts are available to guide you through your solvent cleaner changeover procedures or to advise on equipment.
FURTHER INFORMATION
Please visit our website www.envirotech-europe.com for information about other uses and applications for our vapour degreasing and cleaning products.
Visit www.envirotech-europe.com/applications-and-case-studies for information about uses and applications for all EnviroTech Europe products.
For more advice, please telephone us on +44 (0) 20 8281 6370 or use our contact form. All products are supplied and supported by EnviroTech Europe Ltd. Manufactured in the United Kingdom and available on short delivery times through our dedicated team of distributors worldwide.
Share this page:
Solvent Degreasing and Metal Cleaning
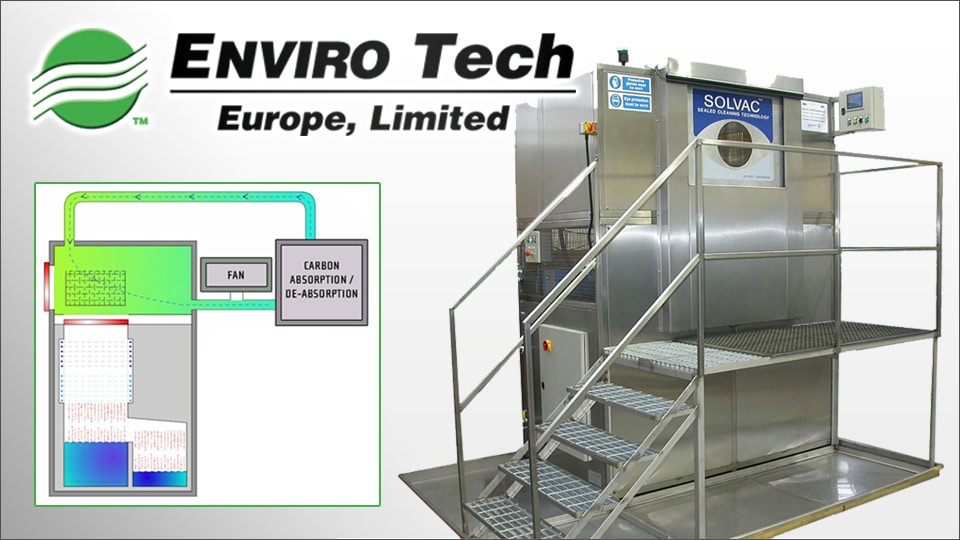
Solvent Degreasing and Metal Cleaning –
Future proof Vapour Degreasing from EnviroTech Europe
Innovation driven by legislation
Vapour degreasing, with or with-out ultrasonics, is the oldest, simplest and most effective solvent degreasing and metal cleaning process used today. It has, until recently, been subject to little change since it was first invented in the early part of the last century. In the UK, Europe, United States and other advanced industrialized economies increasingly stringent legislation to control emissions of VOCs, Global Warming Compounds, Ozone Depleting Compounds, and those compounds associated with human health concerns has led to new formulations for precision cleaning solvents.
Cleaning systems have had to change too. With increased legislation concerning the regulation of health and environmental safety, uses of solvents have been targeted and alternatives are encouraged by the relevant authorities and law makers, often without serious consideration of unintended consequences. For example, water-based cleaning is the obvious alternative but this has many disadvantages compared to vapour degreasing as although the machines are simple and relatively cheap the processes require multiple tanks for immersion or spray processing or long programmed cycles in batch machines for cleaning, rinsing and drying. Water based processes are slow, energy intensive and occupy more floor space than vapour degreasing equivalent where only one tank with small footprint is needed delivering shorter process times and most importantly using minimal energy. Then there is the disposal concern as the used water cannot just be disposed of by pouring it down a drain.
The ideal cleaning process would be vapour degreasing and cleaning with water, but due to the physical characteristics of the vapour/steam and the inability to carry surfactants to remove the oil, grease and soils and the difficulty of rinsing and especially drying this will only ever be a dream.
Halogenated hydrocarbons are the solvents of choice for vapour degreasing and cleaning. The process is essentially simple. A tank with a sump to contain the solvent, heaters at the base and condensation coils around the top section to control the height of the vapour is all that is needed. When heated in the sump halogenated solvents produce, in most cases, a saturated vapour between 3 and 4 times heavier than air at a temperature greater than the ambient temperature of the parts to be cleaned. This allows the solvent vapour to condense on the surface of the parts. The condensate dissolves the contaminants such as oil, greases, flux, and soils returning the used solvent into the sump of the machine for recycling into vapour which continuously condenses onto the parts until they have achieved vapour temperature when, with no further condensation, the process is complete. Parts removed from the cleaning machines are very clean, warm and dry.
The most common halogenated solvents, in use for commercial purposes, are non-flammable so present no risk in this process. Perchloroethylene, used mainly for dry cleaning, methylene chloride previously used widely in paint strippers, 1,1,1- trichloroethane and trichloroethylene used for vapour degreasing were the original materials used based on chlorine chemistry. However continuing concern about the environmental impact and danger to operators by exposure to chlorine-based solvents, especially trichloroethylene, has led to a continuing search for safer alternatives, such as ProSolv 5408e, a trans-1,2-Dichloroethylene based solvent mixture that is non-flammable.
As with all legislation for chemical use regulation and restrictions drive development of associated processes and equipment. The most important developments in vapour degreasing cleaning machines to use solvents for vapour degreasing use two different approaches and raise difficult questions as to which is the best most economical and simplest in use.
The single tank hermetically sealed machines favoured by mainly German manufacturers uses a process tank to contain the solvent and a separate storage tank/vapour generator. Baskets with parts to be cleaned are loaded from the top and lowered into the process tank. A lid then closes over the tank and is hermetically sealed. Solvent is pumped into the process tank. Baskets are immersed in the solvent where agitation, ultrasonics or pumped liquid is circulated through the parts. When the immersion process is complete solvent is pumped to the storage tank and vapour fed to the process tank from a vapour generator for rinsing and drying. Condensing coils/panels controlling the vapour height are linked to coils located within the vapour zone which, when the cycle is complete, collapse the vapour. The process tank is emptied. The saturated air/solvent from the process tank is then recycled through carbon absorption units to remove traces of solvent from the air until the concentration is below 2 grams per cubic meter when the lid opens automatically for the basket of parts, clean and dry, to be removed and replaced with a further basket.
Variations within the hermetically sealed tank are possible using sprays of cold or hot condensed solvent, immersion with or without ultrasonics and revolving baskets to cover most of the problems experienced when processing machined and fabricated parts. Continuous external distillation of the contents of the vapour generator is also an option depending on contamination.
The alternative technology is much simpler and cheaper and less time consuming using well trained techniques. This is favoured by UK based manufacturers. The multilevel system shown in the diagram uses a standard vapour degreasing tank design with a sealed loading section above the process tank.
Work baskets are fed to the load section from a hoist or conveyor. The loading door is then pneumatically sealed to hermetically isolate the process. The sealing lid on the process tank is opened and the basket lowered into the cleaning tank which can be simple vapour degreasing with vapour generator below or an offset generator can be used with the lower section being filled with clean solvent for immersion cleaning with or without ultrasonics or power sprays. Revolving baskets can also be added to improve cleaning in blind or through holes or oil ways in castings and fabrications.
When the process is complete the basket rises to the freeboard area where the condensation coils are located, and parts are allowed to drain and dry. The tank seal opens to allow the basket into the load section while the lid closes again across the process tank. A fan is then activated which produces a negative vacuum in the load area. The loading door is then partially opened to allow a flow of air through the loading section which is exhausted to atmosphere or can be recycled through carbon absorption systems if no external exhaust is preferred. As baskets entering the loading space contain parts drained and dried only very small amounts of solvent are carried in the exhausted air which is monitored to ensure compliance with local legislation. When this is achieved the door opens fully for removal of basket. The loading section can be fitted with top or side sealed doors allowing baskets to flow through on conveyor systems or be loaded from hoists. No solvent enters the work area. Both processes will produce parts cleaned to the highest standards but the choice of which offers the best solution needs a little more consideration.
The single tank process is complicated with the need to move liquids in the machine. It is relatively slow as the carbon adsorption process needs to remove high levels of solvent from the recirculated airstream from the process tank. This is inefficient as adsorption rates for carbon fall rapidly with increasing saturation. Final levels of solvent in the tank when the lid opens will be dragged into the workshop and the area in which the operator is working. Long process cycles reduce throughput.
The simpler multilevel systems where movement of liquids is not required are more efficient and offer much faster process times. Cost of manufacture is also cheaper as no liquid movement is involved. The extracted loading section ensures no leakage of solvent into the work area which offers complete safety for operators and factory staff. The disadvantage of the multilevel machine is the height of the equipment compared to the single tank machine. This will often require the equipment be installed in a pit for easy access.
Both designs of process machines fully comply with the emission regulations of the UK, EU and U.S authorities. Which to choose will depend on many factors which should be discussed with both the equipment and solvent suppliers who have the experience to advise on which offers the best process for the application. Equipment and solvent must work together and it is advisable to ensure that the suppliers work closely together to offer a package with high levels of responsible care and product stewardship to ensure the best and safest installation.
The vapour cleaning process still gives the highest levels of economical cleaning with minimum energy usage, low footprint on the factory floor, safety for the operator, and high production rates with low solvent usage or environmental impact. With the new generation of sealed cleaning machines its future as the process of choice is assured.
Envirotech Europe supplies three distinct products that use this process and we are happy to advise you on the best solution to suit your needs. Please visit our website to find out more about ProSolv 5408e, ProSolv and EnSolv® CC-A.
Image of Solvac hermetically sealed equipment by kind permission of CC Hydrosonics Ltd.
FURTHER INFORMATION
Please visit our website www.envirotech-europe.com for information about other uses and applications for our vapour degreasing and cleaning products.
Visit www.envirotech-europe.com/applications-and-case-studies for information about uses and applications for all EnviroTech Europe products.
For more advice, please telephone us on +44 (0) 20 8281 6370 or use our contact form. All products are supplied and supported by EnviroTech Europe Ltd. Manufactured in the United Kingdom and available on short delivery times through our dedicated team of distributors worldwide.
Share this page:
Electrical corrosion protection
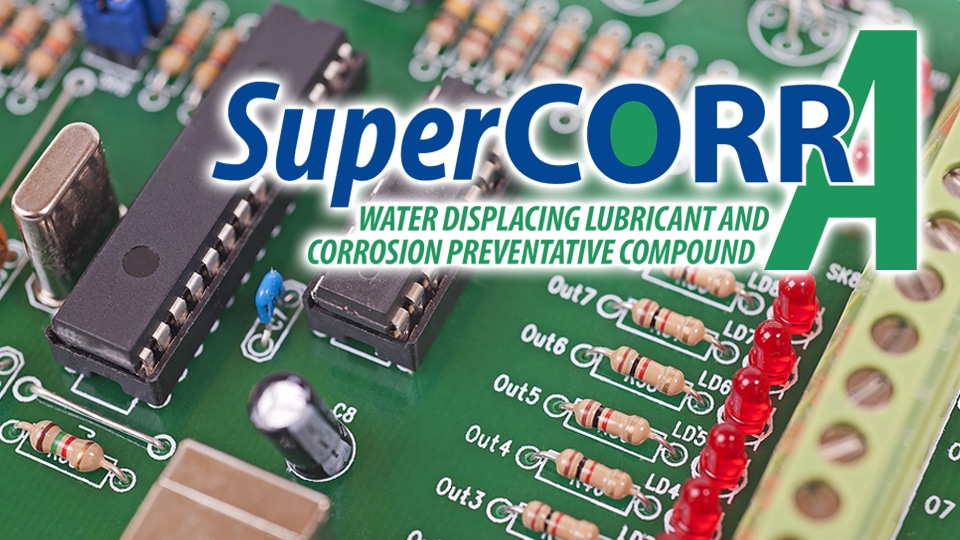
Electrical corrosion protection – Prevent hydrogen sulphide corrosion in electrical and electronic equipment
Super CORR A is a proven and cost-effective way to prevent or inhibit corrosion from destroying electronics and electrical components. Adverse work environments where corrosive gases such as hydrogen sulphide are found, can cause severe corrosion and rapid deterioration of electronic components and equipment, including connectors and switches.
Lost productivity and revenue caused by plant and equipment downtime
Corrosion, in its many forms, costs both private and public sectors hundreds of billions of Euros a year to repair or replace electrical, electronics, or avionic components because of failures caused by corrosion. While all metals corrode, due to a number of different factors, there is no simple or single solution to the overall corrosion problem. However there are some very cost effective and proven ways to prevent corrosion and failures caused by corrosion and thereby reducing or eliminating associated costs and increasing safety which should be foremost in the mind set of any preventative maintenance programme manager.
Super CORR Awas specifically designed to lubricate and prevent corrosion in electrical fittings and connectors; electrical and avionic harness assemblies and connectors; electrical and electronic switches; close tolerance and dissimilar metal components; lighting connectors and sockets. A unique non-flammable “self-healing” ultra-thin film lubricant with a proprietary corrosion preventive compound that will not harden or crack, is not a wax or oil-based product and is formulated without sulphates, chlorides or halogens.
Super CORR A inhibits corrosion caused by exposure to both fresh and salt water moisture as well as the corrosive vapours from Sulphur dioxide (SO2), Nitrogen dioxide (NO2), Hydrogen Sulphide (H2S), Ammonia (NH3), and Chlorine (CL12) based gases found in waste water and sewer treatment plants, pulp and paper mills and plants, chemical and petroleum plants, maritime industry, aircraft/airline industry, military equipment including ships, aircraft, and rolling stock, auto industry, farming and agriculture industry, and the list goes on.
Super CORR A extends the working life of electrical components and systems and other critical items by preventing the deterioration and/or failure caused by corrosion and can significantly reduce downtime, operating and maintenance costs as well as enhance safety. An ultra-thin film, water displacing lubricant and corrosion inhibiting compound Super CORR A has undergone extensive testing by Battelle Labs as well as the U.S. Air Force and meets MIL-DTL-87177B (revised MIL-L-87177A) specification. SuperCORR-A is used by NATO (NATO NSN 8030-99-226-6966) to protect avionic, electrical, electronics, electrical switches and connectors and components from corrosion in both the military and civilian aircraft. Savings for the U.S. government alone is estimated to be in excess of $50 million per year.
Super CORR Aprovides a superior lubrication coefficient and protects components against moisture, wear, general and fretting corrosion, surface static electricity, corona, and other electromigration problems. The super thin non-flammable lubricant film is only 7 microns (0.00028 inch) thick and is formulated to meet the RoHS directive. It is unexcelled in preventing deterioration and contamination on all surfaces of electronic equipment.
The question for you is: What is the cost of NOT using Super CORR A in your preventative maintenance programme?
FURTHER INFORMATION
Please visit our website https://www.envirotech-europe.com/supercorr-a for for information about other uses and applications for Super CORR A.
Visit www.envirotech-europe.com/applications-and-case-studies for information about uses and applications for all EnviroTech Europe products.
Share this page:
ProSolv®5408e vapour degreasing solvent cleaner for flushing refrigeration pipeline systems
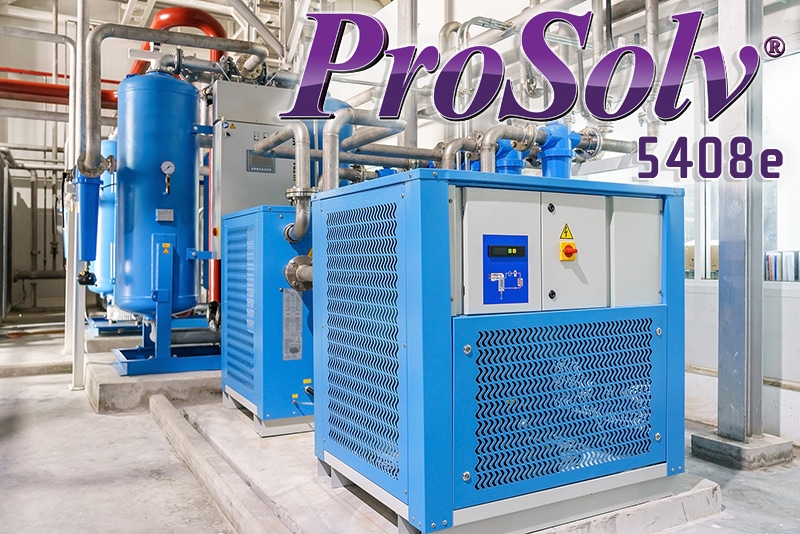
Vapour degreasing solvent cleaner for flushing refrigeration pipeline systems
Concerns connected with the challenging environmental profile of traditional refrigerant gases have led to changes in legislation which are a driving factor in phase-outs and bans on the use of some gases to remove the older materials typically with high ozone depletion (ODP) and global warming potential (GWP). Systems can be replaced or refurbished with new models using compressors able to use more sustainable and acceptable gases. The evolving trend to newer refrigerants continues as the chemistries develop. The refrigerant R-22, which itself was an improvement over earlier refrigerants, is phased out and replaced with R-410a and other alternatives based on HFOs are being marketed.
Retrofitting of current refrigeration systems to accommodate the new developments is not straightforward as most refrigerant gases are not cross-compatible, so the necessity to completely remove all traces of the older versions from the system, including refrigerant lines is essential.
Of course, where possible it’s best simply to replace existing lines with new ones. However, it’s not always possible to do this cost-effectively, especially when the old piping runs under floors or through walls. In such cases thoroughly flushing existing pipework is especially important because even tiny traces of impurities left in the lines can damage new equipment and lead to compressor failure.
THE PERFECT SOLVENT FOR FLUSH CLEANING REFRIGERATION PIPEWORK
Your first step to proper pipework flushing is to select the right solvent. The solvent you choose must be highly effective at dissolving oil grease and other contaminants, to ensure that all residue is removed from the pipes and must be sustainable, environmentally friendly and comply with current legislation.
ProSolv 5408e is the ideal solution to this problem with a profile of properties and advantages making it perfect as your solvent of choice for refrigerant pipeline flushing.
• No flash point Non flammable liquid.
• High specific gravity gives a high soil suspension loading.
• High solvency strength with a KB value of 98.
• Powerful cleaning agent that can flush lines fast, dissolving oil and grease releasing soils from the inner surfaces of pipelines and fittings
• Volatile for fast evaporation. Removing ALL solvent from the pipework after flushing is vital, very volatile so evaporates fast.
• Environmentally responsible. ProSolv 5408e is sustainable and kind to the environment with very low global warming potential, zero ozone depleting potential (ODP).
• Safe for operators when user conditions are followed.
• Economical as it is easily distilled for reuse. No testing or stabilisation required.
PROCEDURE FOR FLUSH CLEANING REFRIGERANT PIPELINES WITH ProSolv®5408e
Of course, simply replacing old piping is the only way to be 100 percent sure that your lines are clean. But in retrofit situations where complete replacement is not possible, flushing the lines with ProSolv 5408e solvent is the best alternative solution for the protection and long working life of your refrigeration system upgrade.
1 – Remove any obstacles. Any equipment and components such as valve, filters and expansion valves that might obstruct the line should be removed prior to the purge.
2 – Pre-flush. This will dislodge any loose debris from the sides of the lines enabling more effective use of the solvent, oil free air or nitrogen at 120 psi is recommended. It’s also good practice to oscillate the pressure to encourage dislodging of debris.
3 – Preparing the pipework. Reducing the length of piping can be more effective due to the pressure loss in long lengths. Section the operation into 15 metre lengths by cutting pipes where necessary. One end of the pipe must be fitted with a connector for the pipe to the nitrogen supply while the exit needs a restrictor valve to allow variable pressures to shock loose particles from internal walls.
IMPORTANT – Flushing with solvent. Refer to ProSolv 5408e Safety Data Sheets for advice on operator protection using solvents.
4 – Safe working. Full PPE with suitable eye protection goggles and gloves must be worn. Solvent fumes are heavier than air and exposure levels can easily be reached working in pits or enclosed spaces. Always institute a ‘buddy system’ and use air fed face masks with attached line.
5 – Delivering solvent. Use a drum pump electric or hand operated with a flexible tube connection for delivering the solvent to the open end of the pipe or tubing to flush the internal surfaces. Using a fresh drum of ProSolv®5408e connect drum pump and the delivery tube to the end of pipe/tube to be cleaned using a pre-fitted screwed or compression fitting.
6 – Drainage and Testing. The drainage end of the pipe or tube should be fitted with a flexible tube into a tank or drain sump allowing samples to be taken in a glass bottle or tube at regular intervals to be sure when no particles or soils are being expelled. The colour of the solvent will change as oil and soluble contaminants are removed and flushing must continue until the flow is totally clear and water white.
7 – Post-flush. ProSolv 5408e solvent is volatile so will dry completely using an oil free airline or nitrogen supply connected to the end of the cleaned pipe/tubing.
8 – A wipe of the pipe/tubing surface at the inlet and outlet using solvent saturated lint free cloth completes the cleaning. If not connected immediately to other parts of the system enclose both ends of cleaned item to prevent recontamination.
Used ProSolv 5408e should not be reused for flushing but can be recovered for reuse by a simple distillation process. Removal from site should use licensed disposal companies.
Further information:
For more information and advice please contact us by telephone on +44 (0) 20 8281 6370 or use our contact form. All products are supplied and supported by EnviroTech Europe Ltd. Manufactured in the United Kingdom and available on short delivery times through our dedicated team of distributors worldwide.
ProSolv 5408e is not just flushing refrigeration pipeline systems,
https://www.vapour-degreasing.com/prosolv5408e/ for information about other applications.
We can provide you with a Material Safety Data Sheets, independent laboratory reports, product samples and technical assistance.
For more information or advice please telephone us on +44 (0) 20 8281 6370 or use our contact form.
All products are supplied and supported by EnviroTech Europe Ltd. Manufactured in the United Kingdom and available on short delivery times through our dedicated team of distributors worldwide.
Share this page:
Related Posts