Latest Articles
The importance of corrosion protection for air conditioning units
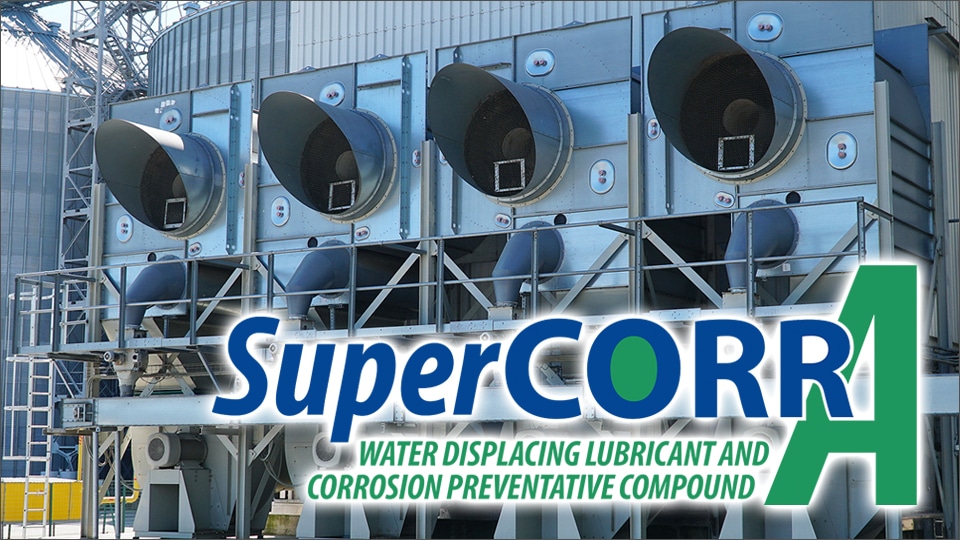
Corrosion protection for air conditioning units.
Corrosion problems in air conditioning units can be caused by various factors including exposure to harsh environmental conditions like humidity, salt, pollutants, chemicals, and other airborne particles, poor maintenance, manufacturing defects or inferior materials, equipment ageing and general wear. To prevent or minimize corrosion in air conditioning units, regular maintenance, proper installation, timely repairs of leaks, and protection against environmental elements are crucial. This includes routine cleaning, inspections, and addressing any issues promptly to extend the lifespan of the AC unit and ensure its optimal performance. Corrosion protection for air conditioning units can be vital in various situations, here are some important considerations:.
Harsh Environments:
In areas near the coast or where the air is laden with salt, the risk of corrosion is higher due to saltwater exposure. Corrosion protection measures, such as coatings or materials designed to resist corrosion, can help extend the lifespan of the air conditioning unit.
High Humidity Environments:
In regions with high humidity levels, the potential for moisture-related corrosion is increased. Protective coatings and treatments can be beneficial in preventing moisture-induced corrosion.
Industrial and Chemical Exposure:
In industrial locations with exposure to corrosive chemicals, protecting air conditioning units from corrosion is important. Acidic or corrosive fumes can deteriorate the unit’s components over time.
Long-Term Maintenance:
Corrosion protection measures can reduce maintenance costs and downtime by preventing or delaying the onset of corrosion-related problems. This is especially important in commercial and industrial applications where HVAC systems are essential for operations.
Extended Equipment Lifespan:
Proper corrosion protection can contribute to the longevity of the air conditioning unit, saving money on replacement costs.
Common methods of corrosion protection for air conditioning units include:
Coatings:
Applying anti-corrosion coatings or paints to the unit’s components to create a barrier.
Galvanized Steel:
Using galvanized steel for components and frames can provide resistance to rust and corrosion.
Regular Maintenance:
Regular cleaning and maintenance to remove corrosive materials like dirt, debris, and salt deposits.
Placement and Enclosure:
Positioning the air conditioning unit in a way that minimizes exposure to harsh elements, or enclosing it in a protective housing, can be effective.
Use of Corrosion-Resistant Materials:
Investing in air conditioning units made from materials that are inherently resistant to corrosion can be a wise choice for long-term durability.
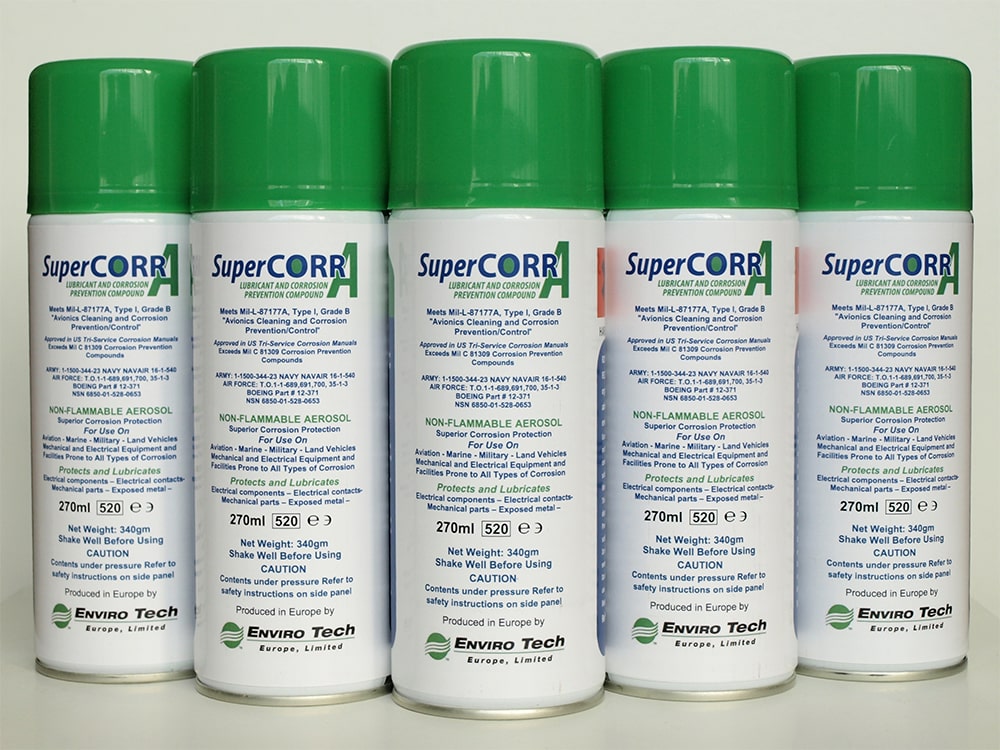
Specialist Barrier Film Corrosion Protection
EnviroTech Europe supplies advanced corrosion protection products, based on approved synthetic materials, to provide quality solutions to a range of lubrication and corrosion problems.
Super CORR A is a unique and proprietary formulation with long-lasting, anti-corrosion inhibitors providing a superior lubrication coefficient and protection against moisture, wear, general and fretting corrosion, static electricity, corona, and other electro migration problems. The non-flammable film is only 7 microns (0.007mm) in thickness, is not a wax or oil-based product and is formulated without sulphates, chlorides, petroleum-based material, or halogens, to meet the EU RoHS directive.
Super CORR A is unexcelled in preventing failures of electrical systems and electronic equipment caused by corrosion as well as preventing the corrosion of metal components surfaces. Use Super CORR A to protect connectors, electrical systems and switches and mechanical controls during servicing. It’s ability to displace water from exposed contacts can ensure reliable operation in extreme conditions, all from one small aerosol can.
The use of Super CORR A for corrosion control can not only bring financial savings in reduced maintenance and replacement costs but more importantly greater safety. It is much simpler and a lot less costly to prevent corrosion than to repair or replace the damaged equipment or component that failed because of corrosion.
Super CORR A is packaged in aerosol cans making access to component parts easy for engineering crews in difficult locations and conditions. Unpainted mild steel will not rust on exterior surfaces directly exposed to sea water environments for at least 6 months, protecting electrical connectors, switches, chains, drive shafts from corrosion while maintaining lubrication on moving surfaces.
EFFICIENT AND ECONOMICAL
- Extremely long-lasting, specially formulated and proprietary anti-corrosive inhibitor.
- Eliminates premature failure of components created by moisture, general or fretting corrosion.
- Prevents deterioration and contamination on all surfaces of electronic and electrical equipment and mechanical close tolerance moving components.
- Reliability increased, maintenance intervals increased and costs reduced, manufacturers save costly warranty service calls or product re-call.
APPROVED
- Industry approval from: NASA, Boeing Aircraft, Bombardier, Embraer, Lear, Gulfstream, Hawker-Beechcraft, Cessna, Raytheon, Polish Airforce, Northrop-Grumman, Royal Navy and Royal Norwegian Air Force.
- Exceeds Mil C 81309 Corrosion Prevention Compounds.
- Approved in US Tri-Service Corrosion Manuals.
FURTHER INFORMATION
Please visit our website https://www.envirotech-europe.com/supercorr-a for for information about other uses and applications for Super CORR A.
Visit www.envirotech-europe.com/applications-and-case-studies for information about uses and applications for all EnviroTech Europe products.
For more advice, please telephone us on +44 (0) 20 8281 6370 or use our website contact form. All products are supplied and supported by EnviroTech Europe Ltd. Manufactured in the United Kingdom and available on short delivery times through our dedicated team of distributors worldwide.
Share this page:
Advantages of using industrial solvent cleaners for the removal of dirt, oil, grease and other contaminants
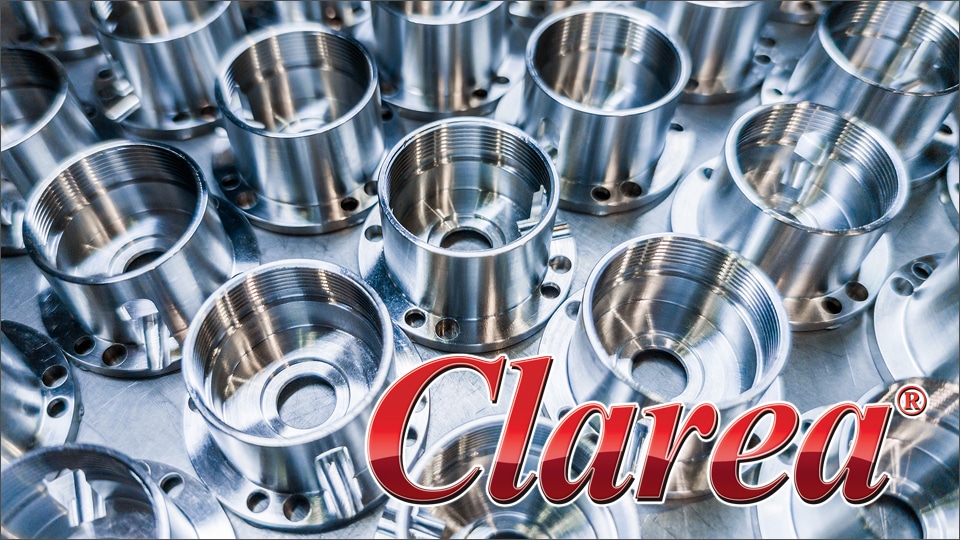
Advantages of using industrial solvent cleaners for the removal of dirt, oil, grease and other contaminants.
Industrial solvent cleaners are specialised cleaning products designed for use in industrial settings. They are formulated to tackle tough and stubborn contaminants found in industrial environments, such as heavy machinery, equipment, tools, and surfaces. They typically contain powerful solvents and cleaning agents capable of breaking down and removing various types of residues, including grease, oil, grime, chemicals, and more.
Organic solvents are used as the primary active ingredient, to dissolve and remove dirt, grease, oil, and other contaminants from surfaces. These chemicals can break down and disperse substances that are not water-soluble. Solvent cleaners are commonly used in various industrial applications for tasks where water-based cleaners are not effective. Industrial solvent cleaners offer several advantages in various applications and industries. The advantages of using industrial solvent cleaners include:
Effective Cleaning:
Industrial solvent cleaners are highly effective at removing a wide range of contaminants, such as grease, oil, paint, adhesives, and more. They can clean surfaces thoroughly, leaving them free from residue and contaminants.
High Solvency:
They have a high solvency power, allowing them to effectively dissolve and remove industrial contaminants that may not be easily cleaned with water-based solutions.
Fast Evaporation:
Many industrial solvent cleaners are formulated to evaporate quickly, leaving behind minimal residue and allowing for rapid cleaning and drying of surfaces.
Versatility:
Solvent cleaners can be used on a variety of surfaces, including metal, glass, plastic, and ceramics. This versatility makes them suitable for different industries and applications. They are often used for degreasing machinery and equipment in manufacturing facilities, automotive repair shops, and other industrial settings.
Fast Drying: Solvent cleaners typically evaporate quickly, leaving surfaces dry and ready for use. This is particularly important in industries where downtime must be minimized.
Precision Cleaning: Solvent cleaners are often used for precision cleaning tasks, such as cleaning electronic components, optical lenses, and medical devices, where cleanliness is critical.
Residue-Free Cleaning: Solvent cleaners are known for leaving minimal to no residue after cleaning, making them ideal for applications where residue could be problematic.
Compatibility: These cleaners are often compatible with a wide range of materials and coatings, reducing the risk of damaging the surfaces being cleaned.
Flammable and Non-Flammable Options: Depending on the specific needs of an application, both flammable and non-flammable solvent cleaners are available, allowing for safer operation in different environments.
Low Surface Tension: Solvent cleaners can penetrate into tight spaces and crevices due to their low surface tension, ensuring thorough cleaning.
Degreasing Capabilities: Industrial solvent cleaners are excellent at degreasing and removing oily residues, making them suitable for automotive, aerospace, and manufacturing industries.
Environmental Considerations: Some industrial solvent cleaners are formulated to be more environmentally friendly, with low VOC (volatile organic compound) and HAP (hazardous air pollutant) content, reducing their impact on the environment.
Regulatory Compliance: Many industrial solvent cleaners are formulated to meet specific industry standards and regulations, ensuring that they are safe and effective for use in various applications.
Long Shelf Life:
Solvent cleaners typically have a long shelf life, allowing for extended storage and usability.
While industrial solvent cleaners offer many advantages, it’s essential to use them with caution, especially those that are flammable, and to follow safety guidelines and regulations to protect workers and the environment. Additionally, it’s crucial to choose the right solvent cleaner for your application to achieve the best results while minimizing any potential drawbacks or risks.
EnviroTech Europe supply high quality hydrocarbon or chlorinated solvent cleaners for the safe removal of dirt, oil, grease and other contaminants
Clarea® industrial solvent cleaners are compatible with all metals, composites and most plastics used to remove dirt, oil, grease, or other contaminants from surfaces without causing harm or leaving residue. They are used as immersion cleaners for component cleaning in manufacturing andengineering industries and as wipe cleaners for large surface areas prior to painting or powder coating.
Clarea® industrial solvent cleaners are aliphatic hydrocarbon based, non-chlorinated, low odour degreasing solvents with specified flash points. They will remove oils, greases, hydraulic fluids cutting fluids and a wide variety of hydrocarbon based protective coatings. Can be safely used with all metals and composites and most plastic and paint finishes.
Clarea HC40 is low odour degreasing fast drying solvent with a flash point of 40°C. It is suitable for ultrasonic and dip systems and can be used with brush or in hand-wipe processes.
Clarea HC62 is a degreasing solvent with a flash point over 60°C. It is suitable for hand-wipe applications when used externally.
Clarea HC96 is a degreasing solvent with a flash point of 96°C. It is suitable for spray or immersion cleaning.
EFFICIENT AND ECONOMICAL
● Versatile and cost-effective solutions for all your industrial cleaning
● Minimal odour and low toxicity for operators
● Multipurpose uses can reduce the inventory of cleaning fluids.
● Flexible uses – evaporation rates suitable for hand wipe, spray, or immersion tank cleaning
● Contains no chlorine, other halogens or stabilisers
● Compatible with all metals and composites and most plastics
● Excellent pre-cleaner for paint or powder coatings
● Safe, reliable, environmentally friendly cleaning
Packaging and availability
Clarea® HC40 and Clarea® HC62 is available in the following container sizes and weights:
205 litre drums, 25 litre cans, 5 litre cans.
We can provide you with a Material Safety Data Sheets, independent laboratory reports, product samples and technical assistance.
For more information or advice please telephone us on +44 (0) 20 8281 6370 or use our contact form.
All products are supplied and supported by EnviroTech Europe Ltd. Manufactured in the United Kingdom and available on short delivery times through our dedicated team of distributors worldwide.
Share this page:
The importance of corrosion protection for electrical systems
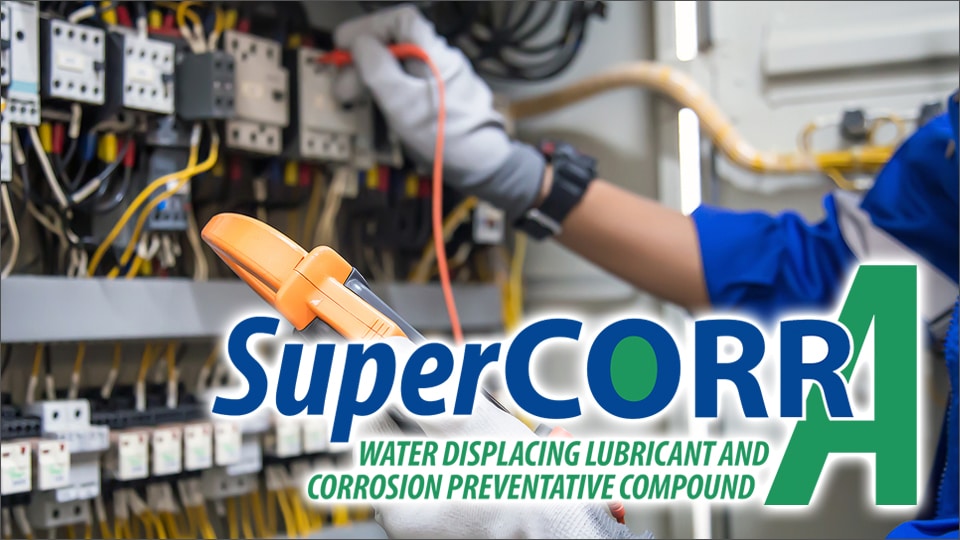
The importance of corrosion protection for electrical systems
Protection from corrosion is vital for safeguarding infrastructure and equipment, reducing costs, ensuring safety, and maintaining the reliability and longevity of critical electrical and electronic systems across various industries. Corrosion protection is critically important for several reasons.
Safety:
Corrosion can compromise the integrity of electrical components, leading to potential safety hazards. Damaged or corroded components can result in electrical short circuits, fires, or other dangerous situations.
Reliability:
Electrical systems are expected to function reliably over extended periods. Corrosion can lead to unexpected failures and downtime, disrupting operations and causing financial losses.
Performance:
Corrosion can degrade the performance of electrical connections, leading to increased resistance and reduced efficiency. This can result in wasted energy, increased operating costs, and reduced system performance.
Longevity:
Proper corrosion protection measures can extend the lifespan of electrical components and systems. By preventing or mitigating corrosion, you can reduce the frequency of maintenance and replacement, saving both time and money.
Energy Efficiency:
Corrosion can increase energy consumption. For example, in HVAC systems, corroded heat exchangers are less efficient, leading to higher energy bills.
Health and Safety:
Corrosion can compromise the safety of equipment and systems, leading to accidents and injuries. For instance, corrosion in the aviation industry can pose a significant risk to flight safety.
Reduced Maintenance Costs:
Dealing with the corrosion related issues listed above can be costly. Preventing corrosion through protective measures is always more cost-effective in the long run than repairing or replacing damaged components. Corrosion protection measures, such as coatings and inhibitors, can reduce the need for frequent maintenance and repair, saving both time and money.
Environmental Impact:
Corrosion can lead to the release of hazardous materials, such as lead, into the environment. Proper corrosion protection measures can reduce the environmental impact of electrical systems.
Economic Impact:
Corrosion costs industries billions of dollars each year in repair, maintenance, and replacement of corroded equipment. Effective corrosion protection measures can significantly reduce these costs.
Maintaining Signal Integrity:
In sensitive electronic systems, corrosion can affect the quality of signals and data transmission. For example, in telecommunications or data centres, corrosion-induced signal degradation can lead to communication errors, false signals or even data loss.
Aesthetic Considerations:
In some cases, electrical systems are visible to the public or customers. Corrosion can be unsightly and negatively impact the image and reputation of an organization.
Preventive Maintenance:
Implementing corrosion protection measures as part of a preventive maintenance program can help identify and address potential corrosion issues before they escalate, minimizing the risk of unexpected failures. Corrosion can cause equipment failures and operational disruptions. Corrosion protection measures ensure the reliable operation of critical electrical systems.
Regulatory Compliance:
In many industries, regulations and standards are in place that require the use of corrosion protection methods to ensure the safety and reliability of electrical systems. This is why Super CORR A is specified in the maintenance manuals for many aircraft manufacturers. Compliance with these regulations is essential to avoid legal and financial consequences.
Overall, corrosion protection is vital for safeguarding electrical and electronic equipment, reducing costs, ensuring safety, and maintaining the reliability and longevity of critical systems across various industries. Common methods of corrosion protection for electrical systems include the use of corrosion-resistant materials, coatings, sealants, periodic inspections, and maintenance, as well as environmental controls to reduce exposure to corrosive elements. Overall, prioritizing corrosion protection is essential for ensuring the safety, reliability, and longevity of electrical systems.
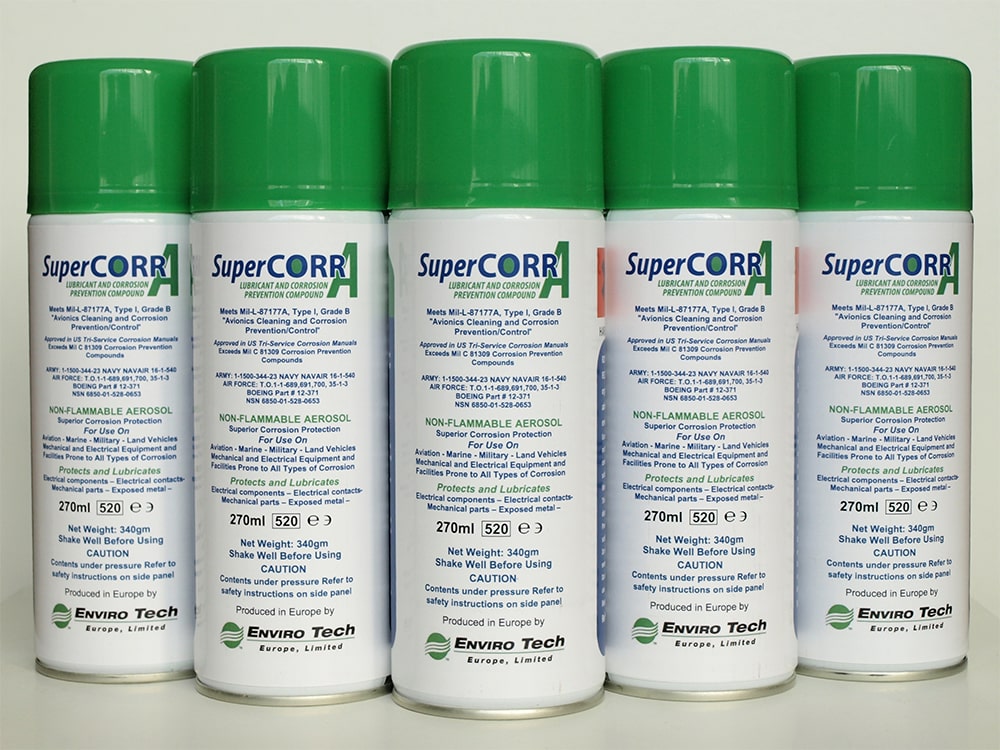
Specialist Barrier Film Corrosion Protection
EnviroTech Europe supplies advanced corrosion protection products, based on approved synthetic materials, to provide quality solutions to a range of lubrication and corrosion problems.
Super CORR A is a unique and proprietary formulation with long-lasting, anti-corrosion inhibitors providing a superior lubrication coefficient and protection against moisture, wear, general and fretting corrosion, static electricity, corona, and other electro migration problems. The non-flammable film is only 7 microns (0.007mm) in thickness, is not a wax or oil-based product and is formulated without sulphates, chlorides, petroleum-based material, or halogens, to meet the EU RoHS directive.
Super CORR A is unexcelled in preventing failures of electrical systems and electronic equipment caused by corrosion as well as preventing the corrosion of metal components surfaces. Use Super CORR A to protect connectors, electrical systems and switches and mechanical controls during servicing. It’s ability to displace water from exposed contacts can ensure reliable operation in extreme conditions, all from one small aerosol can.
The use of Super CORR A for corrosion control can not only bring financial savings in reduced maintenance and replacement costs but more importantly greater safety. It is much simpler and a lot less costly to prevent corrosion than to repair or replace the damaged equipment or component that failed because of corrosion.
Super CORR A is packaged in aerosol cans making access to component parts easy for engineering crews in difficult locations and conditions. Unpainted mild steel will not rust on exterior surfaces directly exposed to sea water environments for at least 6 months, protecting electrical connectors, switches, chains, drive shafts from corrosion while maintaining lubrication on moving surfaces.
EFFICIENT AND ECONOMICAL
- Extremely long-lasting, specially formulated and proprietary anti-corrosive inhibitor.
- Eliminates premature failure of components created by moisture, general or fretting corrosion.
- Prevents deterioration and contamination on all surfaces of electronic and electrical equipment and mechanical close tolerance moving components.
- Reliability increased, maintenance intervals increased and costs reduced, manufacturers save costly warranty service calls or product re-call.
APPROVED
- Industry approval from: NASA, Boeing Aircraft, Bombardier, Embraer, Lear, Gulfstream, Hawker-Beechcraft, Cessna, Raytheon, Polish Airforce, Northrop-Grumman, Royal Navy and Royal Norwegian Air Force.
- Exceeds Mil C 81309 Corrosion Prevention Compounds.
- Approved in US Tri-Service Corrosion Manuals.
FURTHER INFORMATION
Please visit our website https://www.envirotech-europe.com/supercorr-a for for information about other uses and applications for Super CORR A.
Visit www.envirotech-europe.com/applications-and-case-studies for information about uses and applications for all EnviroTech Europe products.
For more advice, please telephone us on +44 (0) 20 8281 6370 or use our website contact form. All products are supplied and supported by EnviroTech Europe Ltd. Manufactured in the United Kingdom and available on short delivery times through our dedicated team of distributors worldwide.
Share this page:
Latest News
SuperCORR A -Advanced corrosion protection for aircraft
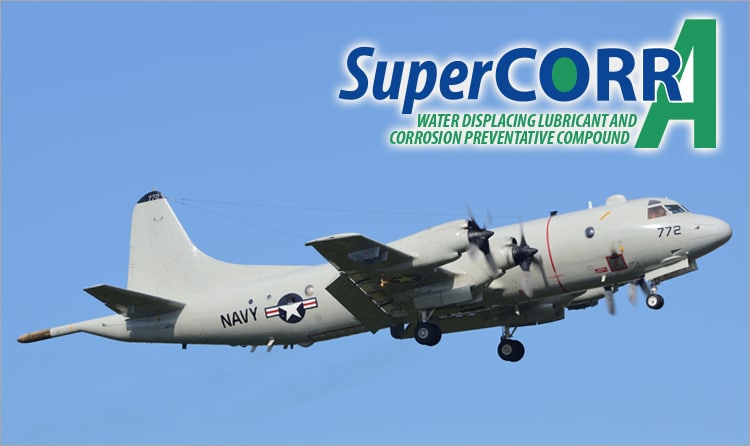
Advanced corrosion protection for aircraft – SuperCORR A lubricates and protects mechanical and electrical flight controls in surveillance aircraft.
Super CORR A provides advanced corrosion protection for aircraft – It lubricates and protects mechanical and electrical flight controls and electronic equipment in Lockheed Martin P-3C Orion aircraft flown by air forces around the world for anti-submarine and maritime surveillance, also used in searches for missing ships or aircraft.
The Royal Australian, Korean and Japanese Air Forces were employed in the search for the Malaysia Airlines flight MH370 Boeing 777 passenger jet which disappeared on a scheduled flight in March 2014. The search for debris in a vast area of ocean, bigger than the land area of Europe, southwest of Perth, Australia operated for thousands of hours at low levels but failed to locate any debris and was suspended in 2017.
The maintenance schedules specify Super CORR A to lubricate and protect the flap tracks and screw jacks in the wings of the aircraft which are constantly exposed to extremely corrosive salt laden air as the aircraft in search mode can be flown at very low altitudes of hundreds of feet for long periods.
Super CORR A lubricant and protective coating is widely used by the military, electrical, electronics and aerospace industries for critical applications to give the protection needed in extreme conditions. Super CORR A deposits a dry protective film with excellent corrosion protection and lubricant properties plus the added advantage of a hydrophobic surface rejecting water that ensures the easiest and best connections for very close spaced connectors, contacts, wiring and moving parts
The U.S. Navy selected Super CORR A after exhaustive testing using American Society for Testing and Materials (ASTM) Standard B117- Standard Practice for Operating Salt Spray Apparatus.
Super CORR A, a Type I, Grade B Corrosion Preventative lubricant out-performed 11 other products in comparative testing to identify the best product to protect and lubricate the flap tracks and screw jacks on the aircraft.
The flap tracks, located in the aircraft’s wings, are what the flaps slide on when they move up or down to lower or increase speed. The screw jacks engage and retract the wing flaps. Corrosion on any of the surfaces can lead to snatching or vibration which can affect the pilot’s control
Due to constant operation in salty and corrosive atmospheres which need post-flight rinses and monthly washing down of the aircraft re-lubrication and corrosion treatment for the flap tracks and screw jacks is required each time, with conventional lubricants, to prevent rusting. Super CORR A was evaluated against competitive products under the Federal Test Method Standard #791B, using a five percent Salt Spray Corrosion Test.
Super CORR A far exceeded the performance of the other products evaluated. After over 200 hours of continuous exposure to salt spray corrosion, Super CORR A protection actually increased over time where all the other, similar, products failed early or contributed to an increase in corrosion.
The accelerated salt fog corrosion testing demonstrated that the application of
Super CORR A which complies with MIL-DTL-87177B (revised MIL-L-87177A) also increased electrical operation to 1400 hours versus 100 hours for the control product used at that time. Technical manuals were updated to include the application for electrical and mechanical parts for civilian and military operations.
The most important conclusion from the historical data and prototype testing is the availability of this excellent corrosion preventive compound that has dry film lubricant properties. The application of Super CORR A on aircraft components can reduce maintenance man hours, reduce part replacement costs, increase life of aircraft, safety, and readiness for operations.
Estimates for the maintenance cost for the US Air Force F-16 fleet can reach $500 million per year, the use at all military branches could reach billions of dollars per year. Applications at locations tested by the U.S. Air Force are not normally treated with corrosion prevention and control lubricants (CPC’s). These are the electrical connectors that are susceptible to subtle and not so subtle forms of corrosion that can interfere with the electrical operation of the F-16.
Testing by the U.S. Navy at NADEP Jacksonville incorporates not only electrical connectors, but mechanical and structural components as well. Future uses will also include ground support equipment. The properties of Super CORR A are such that it can be used in a wide variety of applications and on any materials, metal or plastic. Properties of the Super CORR A far exceed the requirements defined by the MIL-L-87177A specification. Many of the beneficial properties of the product are not required in the MIL specification.
EnviroTech Europe is a manufacturer and distributor of anti-corrosion, lubricants and coatings used on wiring, connectors, switches, circuitry, avionics. Read the full report – ‘Use of MIL-L-87177A as a corrosion prevention compound’ in our Library https://www.corrosion-protect.com/resources
Please visit our website https://www.envirotech-europe.com/supercorr-a for for information about other uses and applications for Super CORR A.
Visit www.envirotech-europe.com/applications-and-case-studies for information about uses and applications for all EnviroTech Europe products.
We can provide you with a Material Safety Data Sheets, independent laboratory reports, product samples and technical assistance.
For more information or advice please telephone us on +44 (0) 20 8281 6370 or use our contact form.
All products are supplied and supported by EnviroTech Europe Ltd. Manufactured in the United Kingdom and available on short delivery times through our dedicated team of distributors worldwide.
Share this page:
Aquus CL-One general purpose industrial cleaning agent

Aquus® CL-One concentrated general purpose industrial cleaning agent –
Non-toxic, water based cleaning and protection of metal surfaces – formulated to offer one solution for all cleaning applications in manufacturing, engineering and general maintenance.
Aquus CL-One is a non-toxic general purpose cleaning agent based on a mixture of surfactants and exhibits a unique combination of characteristics not found in other comparable commercially available products.
Aquus CL-One is formulated to offer ONE SOLUTION for all cleaning applications and reduces time and costs by removing the need for multiple cleaning products usually needed to deal with the challenges presented by the wide range of soils, oils and other contaminants which need to be removed.
Aquus CL-One is biodegradable, non-flammable, non-toxic at used concentrations and, unlike almost all other surfactant systems, is both hydrophilic (water attracting) and oleophobic (oil-repelling).
Aquus CL-One offers excellent emulsion-breaking capability in addition to its unusual combination of properties that makes it so practical for a wide range of industrial applications.
Safe for the environment and users, contains no solvents and is biodegradable within 30 days. One of the innumerable industry specific applications are discussed below but many more will be experienced in day-to-day operations. With only one product for all cleaning applications incorrect selection or dangerous uses can be avoided.
Concentrated Aquus CL-One chemistry is activated by water, varying concentration levels allows the most economical solution to be chosen for specific applications from parts cleaning to surface preparations for finishing or heavier soiling on process machines all from one product. Some of the applications are discussed below.
MANUFACTURING, ENGINEERING and MAINTENANCE
Formulated to tackle the numerous cleaning applications required by the manufacturing and engineering industries. Concentrated Aquus chemistry is activated by water, varying concentration levels allows the most economical solution to be chosen for specific applications from parts cleaning to surface preparations for finishing or heavier soiling on process machines all from one product. Some of the applications are discussed below. Our applications experts and samples of the product are available by completing the contact form.
PARTS AND COMPONENT CLEANING
Ideally suited for cleaning protective coatings, grease and soils from used or parts during manufacturing processes. Aquus CL-One can be used in parts washing equipment or dipping tanks without modifications and leaves no residue after drying. Oil and grease separate from the water and coalesces on the surface of the cleaning solution which can then be skimmed off for recovery and recycling. Precipitated solids free of hydrocarbons can be removed by settlement or in filtration systems. The cleaning solution can be reused continuously within its chemical effectiveness parameters for efficient and economical use.
GENERAL CLEANING
Aquus CL-One is remarkably efficient removing oils, greases, and accompanying dirt from most surfaces. It can be applied by wiping surfaces, mopping floors or in rotary floor cleaning machines, or by low or high-pressure spray. Aquus CL-One is also an effective cleaner in industrial kitchens removing grease and baked on deposits on internal surfaces of ovens and trays. For maintenance of machines, engines etc oil and grease is easily removed pre and post assembly making inspection and repair easier, quicker and cheaper by returning equipment to use.
WASTE TREATMENT SYSTEMS
Aquus CL-One is extremely effective in separating oil, water, and solids in drains and conveyor traps and sumps on automatic honing, turning and grinding machines when using water based lubricant and cooling liquids. The emulsions are broken allowing cleaned metal dust, shavings and dirt to precipitate to the bottom, the solution of Aquus CL-One and water retains the active cleaner in the middle layer, and oil and grease float to the top. The efficiency of oil/water separators in plant waste treatment systems are significantly increased while the amount of toxic waste requiring disposal after treatment is significantly reduced. The cleaning solution can be reused to treat more waste streams until biodegradation occurs and it no longer operates effectively.
FURTHER INFORMATION
Please visit our website https://www.envirotech-europe.com/aquus-cl-one for information about other uses and applications for Aquus CL-One.
Visit www.envirotech-europe.com/applications-and-case-studies for information about uses and applications for all EnviroTech Europe products.
We can provide you with a Material Safety Data Sheets, independent laboratory reports, product samples and technical assistance.
For more information or advice please telephone us on +44 (0) 20 8281 6370 or use our contact form.
All products are supplied and supported by EnviroTech Europe Ltd. Manufactured in the United Kingdom and available on short delivery times through our dedicated team of distributors worldwide.
Share this page:
Aquus CL-One Concentrated all-purpose cleaner
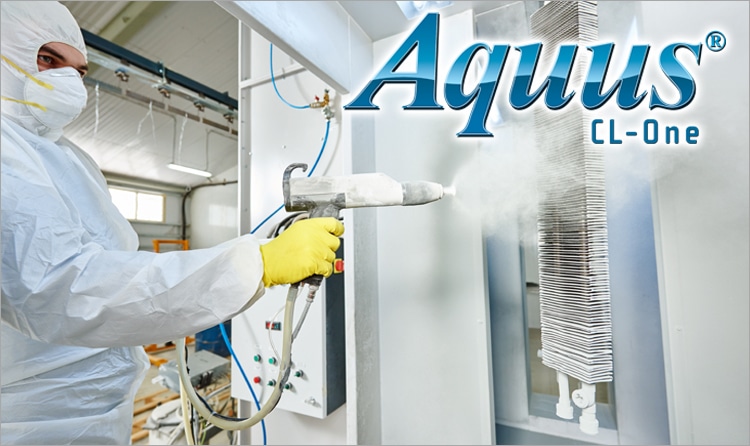
Aquus® CL-One concentrated all-purpose cleaner – Water based cleaning and protection of metal surfaces prior to powder coating or painting.
Aquus CL-One is an excellent all-purpose cleaning system for the cleaning and protection of mild steel and ferrous metal parts which need powder coating or painting immediately or when it is necessary to store unpainted for limited periods. Any cleaning system can be used – hand wiping, dip tanks, ultrasonics or pressure washing.
Uncleaned metal components or fabrications before cleaning are protected by process oils and grease on the metal guarding the surfaces from changes in humidity. Once removed using conventional water-based cleaners flash rusting can occur very quickly during drying.
The unique Aquus CL-One formulation however leaves an invisible barrier on the metal surfaces, after the cleaning process, providing extended corrosion protection during storage, fabrication, or assembly before finishing. The barrier film can be powder coated or painted over without additional rinsing and without affecting adhesion of the coatings.
General purpose cleaning
Aquus CL-One is also an excellent general-purpose concentrated surfactant system containing no solvents which exhibits a unique combination of characteristics that are not found in other commercially available cleaning processes biodegradable, non-flammable, non-toxic at used concentrations and, unlike almost all other surfactant systems, is both hydrophilic (water attracting) and oleophobic (oil-repelling).
Aquus CL-One offers exceptional emulsion-breaking capability in addition to its unusual combination of properties that makes it so attractive for a wide range of industrial applications. In addition to the general cleaner Aquus CL-One, other concentrated cleaners within the range are formulated to offer cleaning solutions for industry specific applications.
One cleaner for all applications
One cleaner for all applications reduces costs by removing the need for multiple cleaning products usually needed to deal with a wide range of soils or contaminants. Safe for the environment and users, containing no solvents is biodegradable within 30 days. Typical with only one product for all cleaning applications incorrect selection or dangerous uses can be avoided.
Please visit our website https://www.envirotech-europe.com/aquus-cl-one for information about other uses and applications.
We can provide you with a Material Safety Data Sheets, independent laboratory reports, product samples and technical assistance.
For more information or advice please telephone us on +44 (0) 20 8281 6370 or use our contact form.
All products are supplied and supported by EnviroTech Europe Ltd. Manufactured in the United Kingdom and available on short delivery times through our dedicated team of distributors worldwide.
Share this page:
Corrosion protection for unpainted metal in highly corrosive environments
Tests demonstrate the amazing properties of SuperCORR A corrosion protection spray to protect unpainted metal surfaces from corrosion
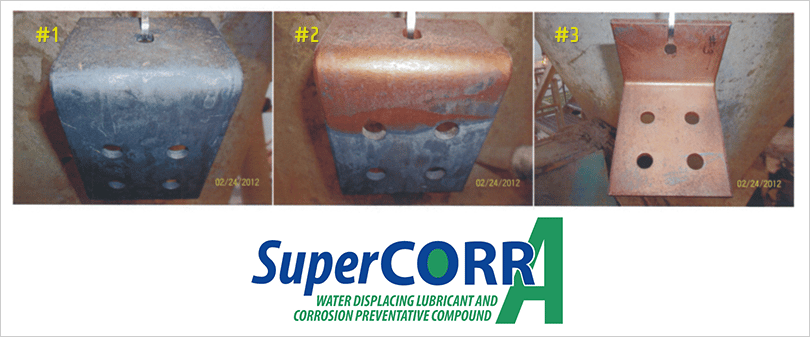
These are photographs of 3 unpainted copper components that were exposed for a month next to the “digester” at a Pulp and Paper Mill. The part marked #1 was the control and not sprayed with SuperCORR A corrosion protection spray. Half of part marked #2 was sprayed with SuperCORR A and half left uncoated. Component #3 was completely treated with SuperCORR A. The main atmospheric corrosion was from hydrogen sulphide (H2S) gas, produced during the cellulose digestion process, which combines with the atmospheric humidity to form a mild acid. Any unpainted or untreated metal surface, copper, brass, mild steel or alloys of zinc and manganese or magnesium will be corroded by this acid when it condenses on the metal surfaces.
This is especially important in electrical motors and power control systems where these metals are used as conductors or switch contacts on printed circuit tracks and all types of connectors which although sealed in control panels will be exposed whenever the boxes are opened or contactors operated and connectors plugged and unplugged. In most cases it is not possible to paint these conductive surfaces or apply other forms of protection without loss of conductivity leading to arcing or supply failures.
These tests demonstrate the amazing properties of SuperCORR A to protect unpainted surfaces from acidic corrosion. As an example, copper and aluminium condensers on water coolers usually last about a month in the acidic environment of pulp production facilities because the corrosive atmosphere around the plant corrodes the metal surfaces on fins and connections.
A trial was set up by the works engineering department at the plant who sprayed a new condenser with an aerosol of SuperCORR A corrosion protection spray. This applies a very thin protective film of a proprietary formulation containing extremely long-lasting anticorrosion inhibitors, which also give superior lubrication coefficients and protect components against moisture. This unique, water displacing lubricant, with synthetic corrosion prevention compounds is tested and proven non-flammable and environmentally friendly without sulphates, chlorides, or other halogens
After a few months the treated condenser showed so little signs of corrosion that further controlled trials were set up to test for long term protection of untreated metal in this extremely corrosive environment experienced in paper and pulp mills, water processing plants and oil drilling rigs.
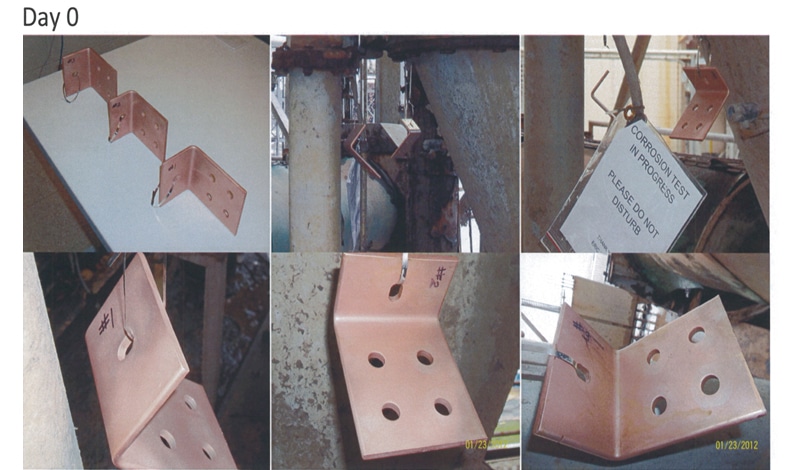
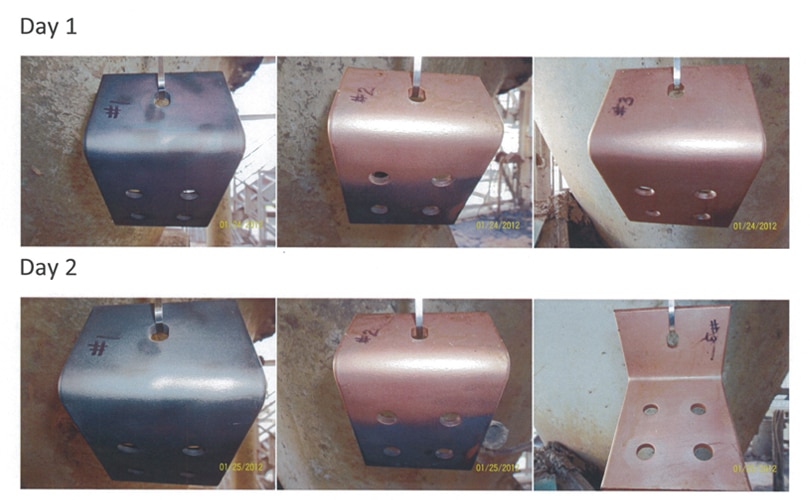
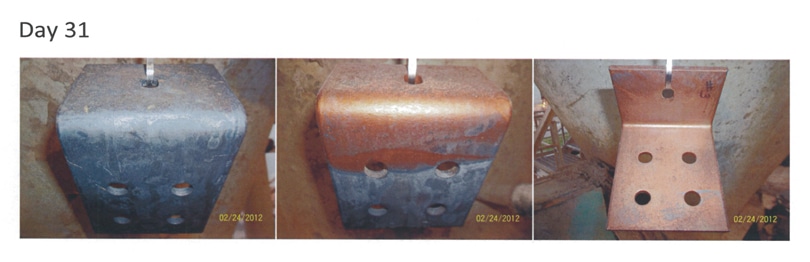
The improvement is clear and demonstrates the savings in costs of parts and labour for maintenance and replacement untreated metal components exposed to these corrosive conditions.
For more information please visit www.envirotech-europe.com/supercorr-a
To discuss the use of SuperCORR A to solve your problems please use the website contact form or phone us, we look forward to hearing from you.
We can provide you with a Material Safety Data Sheets, independent laboratory reports, product samples and technical assistance.
For more information or advice please telephone us on +44 (0) 20 8281 6370 or use our contact form.
All products are supplied and supported by EnviroTech Europe Ltd. Manufactured in the United Kingdom and available on short delivery times through our dedicated team of distributors worldwide.
Share this page:
Cleaning solvent for vapour degreasing in the aerospace industries
ProSolv® 5408 sustainable, economical cleaning solvent for vapour degreasing in the aerospace industries
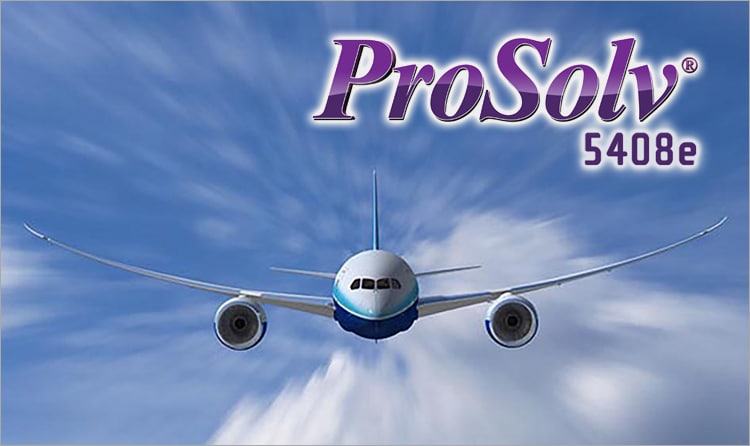
The aircraft and aerospace component manufacturing industries face many critical cleaning applications during manufacturing processes and for finishing where surfaces need to be completely degreased leaving no residues. Although aqueous cleaning would seem to be the method of choice for environmental reasons with new advancements in cleaning solvent chemistry this is often not the case. Vapour degreasing is the most effective process, economical in use with lower energy uses, one tank needing less floor space than multi tank water-based systems and safe for users.
ProSolv 5408e has been developed to be used in place of the traditional chlorinated hydrocarbon solvents, trichloroethylene and perchloroethylene and those based on n-propyl bromide (nPb) which have been phased out for use as vapour degreasing solvents in the EU. The ProSolv 5408e advanced formulation, based on sustainable solvents, has been extensively tested with oils, soils greases and other contaminants from the manufacturing process and with is high KB value all these materials are easily removed to comply with aircraft standards for cleaning and degreasing to the highest levels. No titanium surface cracking or deleterious effects on other metals or composites commonly used for aircraft and aerospace component manufacture have been identified.
The innovative ProSolv 5408e formulation produced by Envirotech Europe ticks all the boxes with the perfect profile for vapour degreasing Soft on the environment with near zero ozone depletion potential (ODP) and very low global warming potential (GWP) its lower boiling point at 48C minimises energy requirements giving reduced process times for greater throughput and comfortably handled critically cleaned parts. The incredibly low surface tension guarantees penetration into micron sized through and blind holes and between close contact surfaces.
Stable in use ProSolv 5408eis safe for users with a high 8hr occupational exposure level of 220ppm. The solvent needs no additives or stabilisers and requires no testing. Sustainable, safe and secure for future use as your forever solvent.
CRITICAL CLEANING FOR THE AIRCRAFT INDUSTRY
A few examples of the many uses are discussed below, our technical service engineers can offer information and advice on critical cleaning in the multitude of other applications experienced in the precision engineering industries.
BONDING OF HONEYCOMB SECTIONS FOR COMPOSITES
An instance of critical cleaning is removal of all contamination from aluminium honeycomb prior to epoxy resin bonding of the formed aluminium skin to produce lightweight high tensile structures for applications such as leading edges on aircraft wings and wind turbine blades. This is an extremely demanding application, as any residues will prevent the adhesion of the adhesives leading to delamination with potentially disastrous effects.
Due to the high standards of cleaning which are required this process is usually carried out by vapour/liquid degreasing with the traditional chlorinated solvents however due to the increasingly stringent controls on these materials ProSolv 5408e which is fully tested to aircraft industry standards and with its greatly improved environmental and user profile is now increasingly used as the sustainable and safer replacement.
CLEANING FOR CRACK AND FAULT TESTING OF WELDS AND CASTINGS
Another common use in the aircraft industry is in the cleaning of castings and metal fabrications before the use of NDT crack detection fluids. Removal of all surface contamination from manufacturing processes is vital to expose faults. Vapour degreasing and vapour liquid cleaning with ultrasonics is a favoured method due to the excellent solubility of oils and greases and other soils using one tank with very fast processing and parts emerging completely clean and dry. Crack and fault detection in casting and welds is also important in other industries such as railways, automotive engines, and turbines where castings or critical welded fabrications are used. This is particularly relevant as part of the maintenance procedure for refurbishment of aircraft landing gear where surfaces can be heavily contaminated by hard to remove hydraulic oils, rubber and cement dust and grease.
Because this application needs completely degreased, residue free and dry surfaces, the use of slow drying cleaners such as hydrocarbons or water-based cleaners may cause problems as the cracks need to be dry to allow penetration of the detection fluids. Vapour degreasing is the most effective cleaning system for all NDT applications as parts emerge dry from the cleaning process. ProSolv 5408e conforms to SaE-AMS2664 and E1417 99-1/7-1-1 solvent precleaning standard for Penetrant testing in aerospace applications.
CRITICAL CLEANING OF OXYGEN AND GAS SYSTEMS
Critical cleaning of oxygen lines and tanks where no organic residues can be tolerated is another ideal use for this new sustainable cleaning solution. ProSolv 5408e conforms to CGA, ELIGA and Compressed Gas Association standards for this application. We have a series of guides to using ProSolv 5408e for component cleaning to Oxygen standards and recommended cleaning methods involved, available on request.
ProSolv 5408e is produced to consistent quality standards worldwide and is available through a network of experienced and qualified suppliers.
For full product information please visit www.vapour-degreasing.com/prosolv5408e
We can provide you with a Material Safety Data Sheets, independent laboratory reports, product samples and technical assistance.
For more information or advice please telephone us on +44 (0) 20 8281 6370 or use our contact form.
All products are supplied and supported by EnviroTech Europe Ltd. Manufactured in the United Kingdom and available on short delivery times through our dedicated team of distributors worldwide.
Share this page:
Related Posts
Corrosion protection for electrical control systems in Wastewater Treatment Plants
SuperCORR A protects electrical control systems against corrosive environments
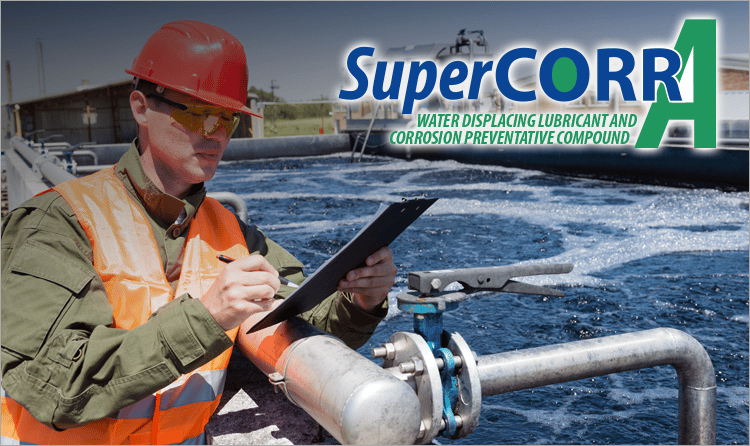
Wastewater treatment plants are subject to corrosion and rust from a variety of causes, one of which is Hydrogen Sulphide gas, (H2S). Corrosion is an insidious and costly problem that causes just about every metal and metal alloy to fail over time. Metals in electrical and electronic control systems, components, connectors, and switches are of most concern.
Corrosion is found in almost all process industries including wastewater treatment plants, pulp and paper mills, fertilizer plants, and numerous other industries and is not going away. Establishing a ‘Preventative Maintenance Program’ that includes corrosion prevention makes it a problem that can be cost effectively dealt with.
One proven and positive way to reduce, if not prevent, corrosion altogether from causing electrical, electronic systems and component failures is by using an ultra-thin film water displacing lubricant material with corrosion inhibiting compound, SuperCORR A has all these properties.
A proprietary formulation packaged in aerosol cans it uses a non-flammable fast drying carrier solvent. The aerosol is supplied with a flexible tube applicator which allows the protective coating to be applied accurately even in difficult to get to components.
Removal of surface contamination from the metallic contact surfaces on switches and circuit breakers is essential to ensure fault free operation. The aerosol uses the unique
SuperCORR A formulation to lift and remove dust and soils from the metal contact surfaces. An inert compound that neither reduces nor increases the electrical conductivity. SuperCORR A also provides long term protection from corrosion and electrical arcing that can lead to shorts and subsequent circuit failures.
Testing SuperCORR A in corrosive environments
SuperCORR A (MIL-DTL-87177B (Revised MIL-L-87177A) Type 1 Grade B lubricant was subjected to extensive and vigorous Mixed Flowing Gas (MFG) testing at Battelle Laboratories under a U.S. Government contract.
Specifications ASTM B827 and ASTM B845 Class III MFG testing protocol were used. This included gases with high corrosion potentials including Hydrogen Sulphide (H2S), Nitrous Oxide(NO2), and Chlorine (Cl2).
ASTM B845 refers to techniques for mixed flowing gas (MFG) tests containing gases that are applied to evaluate devices containing electrical contacts such as slip rings, separable connectors, electromechanical relays or switch contacts. The MFG tests accelerate corrosive degradation processes. Connectors and contacts within closed electronic cabinets may be affected by an environment of different severity than the outside of these cabinets. ASTM B827 outlines procedures for conducting environmental tests involving exposures to controlled quantities of corrosive gas mixtures. Equipment and methods for gas, temperature, and humidity control for tests to be conducted in a reproducible manner are described.
Reproducibility is measured using control coupons whose corrosion films are evaluated by mass gain, coulometry, or by various electron and X-ray beam analysis techniques. Reproducibility can also be measured by in situ corrosion rate monitors using electrical resistance or mass/frequency change methods. Full copies of these tests can be made available on request.
Industrial applications
SuperCORR A has a proven performance record in protecting electrical components, systems, connectors and electronics. The coating will also prevent the ingress of moisture and other contaminants onto the connector surfaces. These initiate corrosions and cause intermittent component failure or a premature degradation of component performance.
The Battelle Laboratories studies provided data and related processing information validating the benefits of using SuperCORR A. to protect the electrical connectors of line replacement units (LRUs) used in military aircraft avionic applications.
The results of the laboratory and field-testing activities conducted in these studies confirm that SuperCORR A is an extremely effective coating to protect electronics, electrical components and systems including switches and connectors with no compromise of the integrity of the electrical component/system even in very corrosive environments.
As a result of testing on site at a number of private and public companies with the confirmatory work at Battelle Laboratories SuperCORR A is being used to reduce maintenance and repair costs in a range of different industrial applications – wastewater treatment plants, pulp and paper mills, automotive and heavy equipment industries and in the power production sector oil and gas and renewable energy and in both the aviation and maritime industries.
FURTHER INFORMATION
Please visit our website www.envirotech-europe.com/supercorr-a for information about other uses and applications. For more advice, please telephone us on +44 (0) 20 8281 6370 or use our website contact form.
All products are supplied and supported by EnviroTech Europe Ltd. Manufactured in the United Kingdom and available on short delivery times through our dedicated team of distributors worldwide.
We can provide you with a Material Safety Data Sheets, independent laboratory reports, product samples and technical assistance.
For more information or advice please telephone us on +44 (0) 20 8281 6370 or use our contact form.
All products are supplied and supported by EnviroTech Europe Ltd. Manufactured in the United Kingdom and available on short delivery times through our dedicated team of distributors worldwide.
Share this page:
Related Posts
Critical cleaning of electronics and electrical components
ProSolv® 5408 new sustainable solvent for critical cleaning of electronics and electrical components
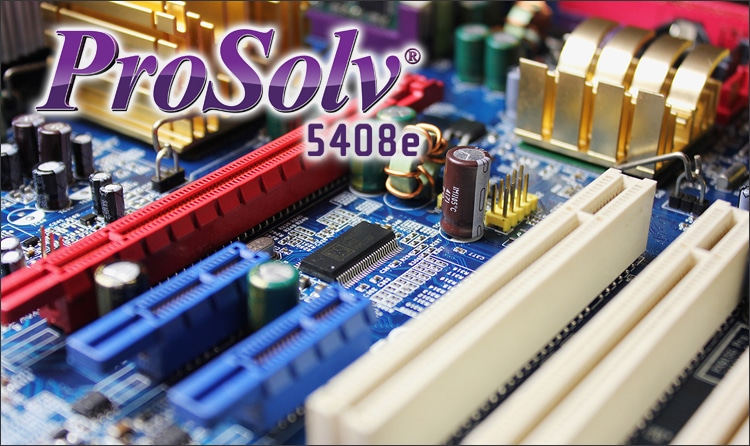
Solvents are used throughout industries where extremely high performance and safety critical cleaning levels are required including aerospace, military and defence, electronics, semiconductor manufacturing, optics, and industrial machining.
ProSolv 5408e is an innovative contemporary highly effective, versatile defluxer developed to not only remove rosin flux, no-clean flux, oil, grease and wax contaminants, but also to eliminate residual halide salts, ions and other polar and non-polar soils and contaminants that often cause component failures with tracking and other issues impacting performance.
Solvents based on conventional chlorinated hydrocarbons have delivered the high standards required for critical cleaning in the past. These chemicals had desirable properties which when combined gave a profile which was perfect for vapour/vapour liquid degreasing when combined with suitable equipment as industrial cleaning systems.
Non-flammable, consistent azeotropes, low viscosity, high liquid density, very low surface tension, and effective wetting enabling them to penetrate tight spaces for optimum cleaning performance. High KB values allows for cleaning a variety of light and heavy soils including particulates, ionic soils, oils, waxes, and greases these are no longer acceptable.
Evolving legislation for ecodevelopment demanded by governments worldwide demand inventive and original formulations for the use of solvents to continue to comply with the increasingly stringent legislation for protection of the environment and, even more importantly, safety of operators who maybe exposed to the products. In applications where formulated blends of halogenated solvents have been used very effectively in the past these are now required by changes in legislation to be phased out of use.
With their 25 years wealth of experience in this field as the inventors of the highly regarded n propyl bromide (nPB) based EnSolv range of precision cleaning solvents EnviroTech Europe created a contemporary new formulation based on recent research and developed a new solvent as a replacement for the “old” technology which has been found to perform just as effectively, but without the negative environmental, health and safety issues.
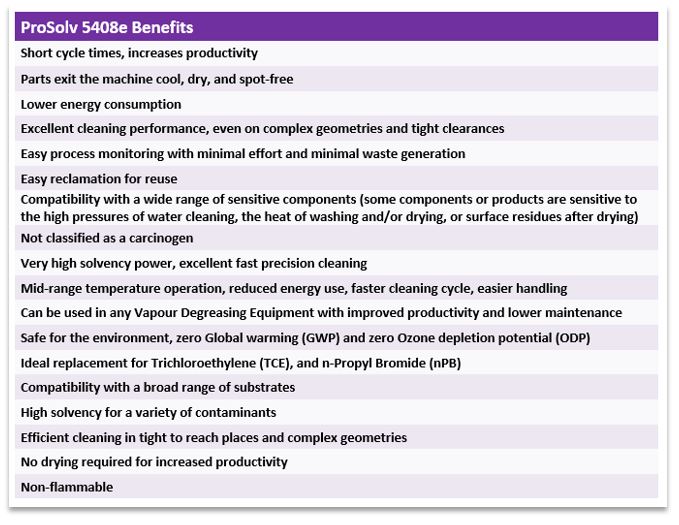
Listed above are just some of the benefits from using ProSolv 5408e, your forever sustainable solvent for cleaning and defluxing in the electronics and electrical components industry and an economical and efficient “drop in “for vapour / vapour liquid cleaning systems using legacy solvents. EnviroTech experts with many years of experience are available to guide you through changeover procedures or to advise on equipment.
For full product information please visit www.vapour-degreasing.com/prosolv5408e
We can provide you with a Material Safety Data Sheets, independent laboratory reports, product samples and technical assistance.
For more information or advice please telephone us on +44 (0) 20 8281 6370 or use our contact form.
All products are supplied and supported by EnviroTech Europe Ltd. Manufactured in the United Kingdom and available on short delivery times through our dedicated team of distributors worldwide.
Share this page:
Related Posts
Medical Device Cleaning
ProSolv® 5408 high performance vapour degreasing solvent for medical device cleaning
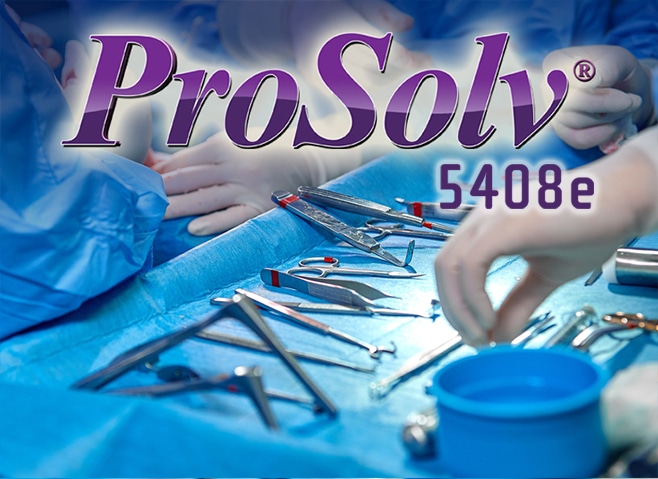
Medical device cleaning
Critical cleaning is vital throughout the medical supply industry for safe, successful operations and procedures. Manufacturers of medical instruments, implants and other devices using metals, glass, ceramics and plastics must select a cleaning processes compatible with all these materials of construction, to remove oils and other contaminants from the manufacturing processes. The cleaning system must be proven to be safety critical and to leave no residues on the surfaces of the cleaned parts.
In this short article we discuss the benefits of condensation cleaning with ProSolv 5408e vapour degreasing solvent for medical device cleaning compared to water-based cleaning.
Water based cleaning options
Formulations for water based cleaners use combinations of surfactants to reduce the very high surface tension of water to allow penetration of the cleaning solution into minutes holes and very fine mechanical clearances. The solutions must solubilise oils, greases, cutting fluids, grinding and buffing compounds and remove particulate soils. Biocides are also present in these formulations to ensure no bioburden is carried over from the cleaning process.
After cleaning residues of chemicals must be removed or they may be a source of corrosion when the devices are in use. Multiple rinses in hot and cold de-ionised water using agitation of baskets or carriers or ultrasound to dilute and displace the cleaning liquids retained in minute holes, cavities and trapped between close tolerance metal surfaces.
Continuous production of high-quality deionised rinse water is extremely expensive, but the drying process is even more costly and environmentally challenging. Multiple cleaning and rinse tanks and drying ovens or tunnels need a lot of space and energy. Further controlled conditions are needed to cool parts after drying to prevent condensation of moisture, which can be growth media for bacteria, on the critically clean surfaces, before packing in sterile bags and containers for storage or shipping.
High output water based cleaning equipment can use conveyorised high pressure targeted spray tunnels for automated high-volume production with integrated “blow off” drying and conditioning tunnels.
For smaller scale operations systems are available using baskets in single cell dishwasher type equipment or open tanks. The latter can use manual or automated handling to progress baskets through the cleaning cycle using similar aqueous based chemical formulations with multiple deionised water rinses and a separate drying oven. These systems can process several baskets or carriers at a time so are only suitable for small batch production. In either case long process times will determine the size and complexity of installations.
Compare the complications of water-based processing to the simplicity and speed of vapour degreasing using ProSolv® 5408e solvents
Vapour degreasing or more properly condensation cleaning, is a proven process where a non-flammable halogenated solvent, safe for people and the environment is heated in the sump of a tank. Boiling solvent produces a dense vapour which is contained by condensation coils around the inner surfaces at the top of the tank. Solvent condensed on the coils is returned to the sump for reuse in a closed cycle.
Parts to be cleaned at ambient temperature are immersed in the vapour which condenses as solvent on the surfaces of the devices or parts in a continuous stream of perfectly clean solvent until the surfaces reaches vapour temperature when condensation ceases. Vapour degreasing uses only one tank with one liquid. Parts are cleaned, rinsed and dry in 3 to 5 minutes with parts hand hot ready for further processing, storage or packing into sterile packs for shipping.
ProSolv 5408e solvents were developed to provide superior critical cleaning performance for manufacturers of medical devices and equipment. The solvent is stable when used for vapour degreasing or cold dip cleaning and compatible with metals, including titanium, ceramics, glass and most plastics used in producing orthopaedic implants, dental, ophthalmic and surgical tools, lenses etc. ProSolv 5408e is a cost effective and sustainable solution to remove polar and non-polar soils and other contaminants and sets the standard for removal of machining and cutting oils, coolants, greases, grinding, buffing and polishing compounds, while leaving no residue.
Vapour degreasing and dip cleaning with ProSolv 5408e is a very effective steriliser of microbial contaminants. Exposing the microorganisms, which have cell walls made up of organic materials including lipids (Fats), to a powerful solvent is a very efficient disruptor of the cell walls. Once compromised the organism’s inner workings lose this protection and the organism dies reducing the bioburden.
ProSolv 5408e is also an excellent solvent carrier for organic or synthetic medical lubricant. This application for coating needles, cannulas and instruments needs consistent quality and evaporation rate to produce, comfortable, pain free insertion for patients.
In many medical applications oxygen and gas supply systems are needed and cleaning at installation and when extensions of pipework and fittings are added is vital for safety. ProSolv 5408e removes oil and organics leaving residue free, dry surfaces to standards approved by gas supply companies, and is compatible with all metals.
Clearly solvent cleaning and vapour degreasing with ProSolv 5408e is a better choice than water cleaning. Faster throughput, lower costs and sustainability to meet the unique challenges in achieving the high standards demanded for medical device manufacturing.
ProSolv 5408e is manufactured in UK with excellent customer service, technical support and training from qualified distributors throughout Europe.
For full product information please visit www.vapour-degreasing.com/prosolv-medical
We can provide you with a Material Safety Data Sheets, independent laboratory reports, product samples and technical assistance.
For more information or advice please telephone us on +44 (0) 20 8281 6370 or use our contact form.
All products are supplied and supported by EnviroTech Europe Ltd. Manufactured in the United Kingdom and available on short delivery times through our dedicated team of distributors worldwide.
Share this page:
Related Posts