Latest Articles
Why are vapour degreasing solvents so good at cleaning?
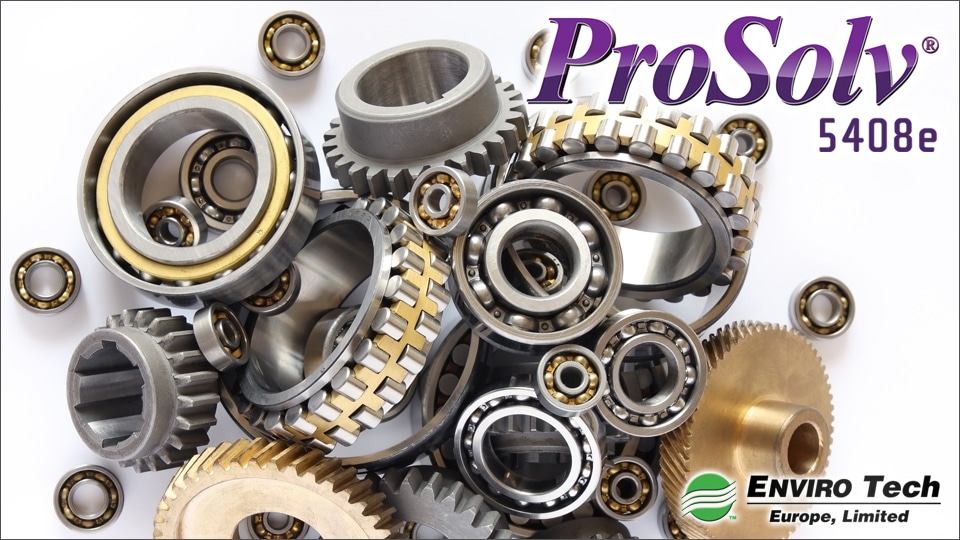
Why are vapour degreasing solvents so good at cleaning?
Vapour degreasing solvents are typically chosen for their excellent solvency properties. They have the ability to dissolve and disperse a wide range of contaminants, including dirt, oil, grease, wax, and other contaminants. The cleaning action of solvents is primarily attributed to their unique molecular properties and interactions with the materials they contact. Here’s why solvents are so good at cleaning:
Low Surface Tension:
Vapour degreasing solvents can reduce the surface tension of liquids, making them more effective at penetrating and breaking up dirt and stains. This allows the solvent to reach areas that might otherwise be hard to clean.
Polarity:
The polarity of a solvent plays a significant role in its cleaning ability. Polar solvents have molecules with positive and negative poles, which allows them to interact with polar substances like water-based stains. Nonpolar solvents, on the other hand, are effective at dissolving nonpolar substances like oils and grease. Different cleaning tasks may require the use of polar or nonpolar solvents depending on the nature of the dirt or stain. Most vapour degreasing solvents are nonpolar in nature, meaning they do not have a positive or negative charge. This allows them to interact with a variety of contaminants, regardless of their charge or polarity, making them versatile for different types of cleaning applications.
Heat and Vaporization:
The vapour degreasing process involves heating the solvent to create vapour, which rises and condenses on the surfaces to be cleaned. This condensation releases latent heat, which aids in loosening and lifting contaminants from the surfaces. The vaporization and condensation cycles help dislodge and carry away dirt, oils, and other substances effectively.
No Aqueous Residues:
Unlike water-based cleaning methods, vapour degreasing solvents leave little to no aqueous residue behind. This is especially important for applications where water could cause corrosion or damage, such as cleaning sensitive electronics or precision mechanical components.
Minimal Agitation Required:
Vapour degreasing is a relatively gentle cleaning method that doesn’t require extensive mechanical agitation. This reduces the risk of damaging delicate parts while ensuring effective cleaning.
Consistency:
Vapour degreasing provides consistent and uniform cleaning results because the solvent vapor can reach all surfaces evenly, including intricate and complex geometries.
Environmental Considerations:
While some vapour degreasing solvents in the past were environmentally concerning, modern solvents are designed to be safer and more environmentally friendly. They are engineered to have lower toxicity, reduced volatility, and minimal global warming or ozone-depleting potential.
Dissolving Power:
Solvents have the ability to dissolve a wide range of substances, both organic and inorganic. This is due to their molecular structure, which allows them to interact with different types of molecules. When a solvent comes into contact with a substance, its molecules surround and separate the particles of the substance, breaking down the intermolecular forces holding them together. This leads to the dissolution of the substance into the solvent.
Evaporation:
Vapour degreasing solvents typically have relatively low boiling points, which means they evaporate quickly when exposed to air. This evaporation helps in removing the dissolved dirt and contaminants from surfaces, leaving them clean and dry. It is important to ensure evaporating solvent doesn’t escape to the atmosphere. This is achieved by having cold condensing coils just above the components being cleaned.
Versatility:
Vapour degreasing solvents come in various types and compositions, allowing them to target specific types of contaminants. For example, alcohol-based solvents are effective at cleaning glass surfaces due to their ability to dissolve and evaporate quickly without leaving streaks.
Chemical Interactions:
Vapour degreasing solvents can undergo chemical reactions with certain types of substances, leading to their removal or transformation. This can be especially useful for removing tough stains that might not be easily removed through simple dissolution.
Compatibility:
Vapour degreasing solvents are often formulated to be compatible with specific materials, ensuring that they don’t damage the surfaces being cleaned. This makes them versatile for use on a wide range of surfaces.
Rinsing Action:
Vapour degreasing solvents can also act as rinsing agents, carrying away dissolved dirt and contaminants when they evaporate. This helps prevent redeposition of dirt onto cleaned surfaces.
Overall, the combination of excellent solvency, low surface tension, nonpolar properties, heat assistance, minimal residue, and controlled vaporization make vapor degreasing solvents highly effective for a wide range of cleaning applications.
It’s important to note that while solvents are effective cleaning agents, their use should be handled with care. Some solvents can be toxic, flammable, or harmful to human health and the environment, so proper precautions and guidelines should be followed when using them. Additionally, choosing the right solvent for a specific cleaning task is crucial to achieve optimal results without causing damage to the surfaces being cleaned.
Zero Ozone Depletion Potential (ODP) and very low Global Warming Potential (GWP) solvent cleaner for high performance vapour degreasing
ProSolv® 5408e has been developed to provide superior critical cleaning performance for manufacturers of electronic and electrical components. High Solvency (KB Value 98) for removal of organic residues, compatible with organic and synthetic oils and most plastics and metals.
ProSolv® 5408e is a high-performance solvent cleaner used for sustainable and future proof vapour degreasing. It has a GWP of less than 1, with a 100 year Integrated Time Horizon (ITH). Soft on the environment and safe for users, it offers improved cleaning at lower costs.
ProSolv® 5408e ticks all the boxes and is the perfect profile for a modern vapour degreasing solvent. Exceptionally low surface tension to penetrate micron sized holes and close contact surfaces. Sustainable and secure for the future. Non-carcinogenic, low boiling point, economical with energy with low solvent losses, faster production, reduced costs, easy handling.
EFFICIENT AND ECONOMICAL
- Fast precision cleaning with short cycle times.
- Can be used in any vapour degreasing equipment, lower energy consumption and lower maintenance.
- Ideal replacement for Trichloroethylene, n-Propyl Bromide, Perchloroethylene and HCFC based solvents.
- Stable with no additives, no testing required.
- Improved productivity, parts exit the machine cool, dry and spot-free with no drying required.
- Minimal non-volatile residue (>10ppm).
- High density solution, excellent for ultrasonic cleaning.
- Mid-range boiling point (46°C).
- Very low surface tension for penetration into the micron level crevices and holes, efficient cleaning in tight to reach places and complex geometries.
- Easy process monitoring with minimal effort and minimal waste generation, easy reclamation for reuse.
- High Solvency (KB Value 98) for a variety of contaminants.
- Compatible with a broad range of substrates.
SAFE FOR USERS AND THE ENVIRONMENT
- Safe for the environment, Zero Ozone Depletion Potential (ODP).
- Very low Global Warming Potential (GWP)
- GWP of less than 1, AR4 100yr Integrated Time Horizon (ITH).
- Non-hazardous for transportation.
- Non-flammable (No Flash Point).
- Not classified as a carcinogen
Listed above are some of the benefits from using ProSolv® 5408e, a sustainable vapour degreasing solvent for precision cleaning and an economical and efficient replacement solution for cleaning systems using older legacy solvents, which are now either banned or being phased out. EnviroTech Europe have many years of experience and our experts are available to guide you through your solvent cleaner changeover procedures or to advise on equipment.
FURTHER INFORMATION
Please visit our website https://www.envirotech-europe.com/prosolv5408e for information about other uses and applications for ProSolv 5408e.
Visit www.envirotech-europe.com/applications-and-case-studies for information about uses and applications for all EnviroTech Europe products.
For more advice, please telephone us on +44 (0) 20 8281 6370 or use our website contact form.
All products are supplied and supported by EnviroTech Europe Ltd. Manufactured in the United Kingdom and available on short delivery times through our dedicated team of distributors worldwide.
Share this page:
Related Posts
The advantages of using fluorinated solvents
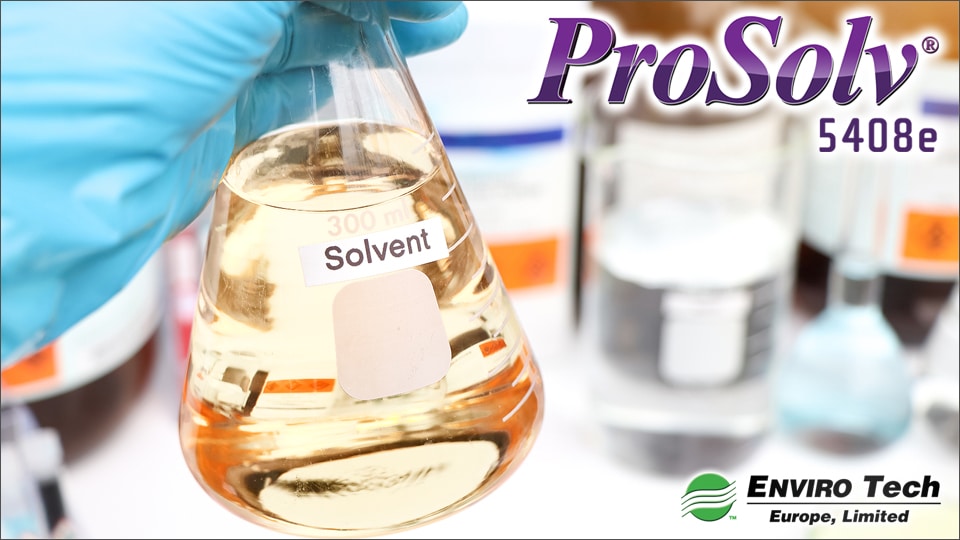
The advantages of using fluorinated solvents for your vapour degreasing process
Fluorinated solvents, also known as fluorocarbon solvents, offer several advantages in various industrial and scientific applications, including being highly suited for vapour degreasing. Here are some of the key advantages of using fluorinated solvents:
Environmental Compatibility:
Fluorinated solvents are often chosen as alternatives to more hazardous solvents due to their relatively low impact on the environment. They have low ozone depletion potential (ODP) and negligible global warming potential (GWP). Additionally, they have low toxicity and are not classified as hazardous air pollutants (HAPs).
Chemical Stability:
Fluorinated solvents exhibit excellent chemical stability, making them highly resistant to degradation and reactions with other chemicals. They are compatible with a wide range of materials, including metals, plastics, and elastomers. This stability allows for their use in challenging environments and with reactive substances.
Solvency Power:
Fluorinated solvents have strong solvency power, meaning they can dissolve a wide range of organic and inorganic compounds. This property makes them effective in applications such as cleaning, degreasing, and precision cleaning, where the complete removal of contaminants is crucial, such as cleaning to oxygen standard.
Nonflammability:
One of the significant advantages of fluorinated solvents is their non-flammable nature. Under testing to ASTM D 93 they will not flash and therefore do not support combustion, making them safer to use compared to many traditional solvents. This property reduces the risk of fire hazards in various industrial processes and applications.
Dielectric Properties:
Fluorinated solvents have excellent dielectric properties, making them ideal for applications that require electrical insulation and heat transfer. They are commonly used in electronic and electrical industries for tasks such as cleaning electrical components, cooling electronics, and as a dielectric fluid in transformers and capacitors.
Thermal Stability:
Fluorinated solvents can withstand a wide range of temperatures without decomposing or losing their properties. This thermal stability allows them to be used in high-temperature applications, including heat transfer fluids, lubricants, and as coolants in various industrial processes.
Surface Tension Control:
Fluorinated solvents have the ability to modify the surface tension of liquids, enabling them to spread evenly and improve wetting. This property makes them useful in applications such as coatings, adhesives, and printing, where uniform and controlled wetting is required.
Zero Ozone Depletion Potential (ODP) and very low Global Warming Potential (GWP) solvent cleaner for high performance vapour degreasing
ProSolv® 5408e has been developed to provide superior critical cleaning performance for manufacturers of electronic and electrical components. High Solvency (KB Value 98) for removal of organic residues, compatible with organic and synthetic oils and most plastics and metals.
ProSolv® 5408e is a high-performance solvent cleaner used for sustainable and future proof vapour degreasing. It has a GWP of less than 1, with a 100 year Integrated Time Horizon (ITH). Soft on the environment and safe for users, it offers improved cleaning at lower costs.
ProSolv® 5408e ticks all the boxes and is the perfect profile for a modern vapour degreasing solvent. Exceptionally low surface tension to penetrate micron sized holes and close contact surfaces. Sustainable and secure for the future. Non-carcinogenic, low boiling point, economical with energy with low solvent losses, faster production, reduced costs, easy handling.
EFFICIENT AND ECONOMICAL
- Fast precision cleaning with short cycle times.
- Can be used in any vapour degreasing equipment, lower energy consumption and lower maintenance.
- Ideal replacement for Trichloroethylene, n-Propyl Bromide, Perchloroethylene and HCFC based solvents.
- Stable with no additives, no testing required.
- Improved productivity, parts exit the machine cool, dry and spot-free with no drying required.
- Minimal non-volatile residue (>10ppm).
- High density solution, excellent for ultrasonic cleaning.
- Mid-range boiling point (46°C).
- Very low surface tension for penetration into the micron level crevices and holes, efficient cleaning in tight to reach places and complex geometries.
- Easy process monitoring with minimal effort and minimal waste generation, easy reclamation for reuse.
- High Solvency (KB Value 98) for a variety of contaminants.
- Compatible with a broad range of substrates.
SAFE FOR USERS AND THE ENVIRONMENT
- Safe for the environment, Zero Ozone Depletion Potential (ODP).
- Very low Global Warming Potential (GWP)
- GWP of less than 1, AR4 100yr Integrated Time Horizon (ITH).
- Non-hazardous for transportation.
- Non-flammable (No Flash Point).
- Not classified as a carcinogen
Listed above are some of the benefits from using ProSolv® 5408e, a sustainable degreasing solvent for precision cleaning and an economical and efficient replacement solution for cleaning systems using older legacy solvents, which are now either banned or being phased out. EnviroTech Europe have many years of experience and our experts are available to guide you through your solvent cleaner changeover procedures or to advise on equipment.
FURTHER INFORMATION
Please visit our website https://www.envirotech-europe.com/prosolv5408e for information about other uses and applications for ProSolv 5408e.
Visit www.envirotech-europe.com/applications-and-case-studies for information about uses and applications for all EnviroTech Europe products.
For more advice, please telephone us on +44 (0) 20 8281 6370 or use our website contact form.
All products are supplied and supported by EnviroTech Europe Ltd. Manufactured in the United Kingdom and available on short delivery times through our dedicated team of distributors worldwide.
Share this page:
Related Posts
General purpose industrial cleaning solvents
Clarea® general purpose industrial cleaning solvents for safe removal of dirt, oil, grease and other contaminants
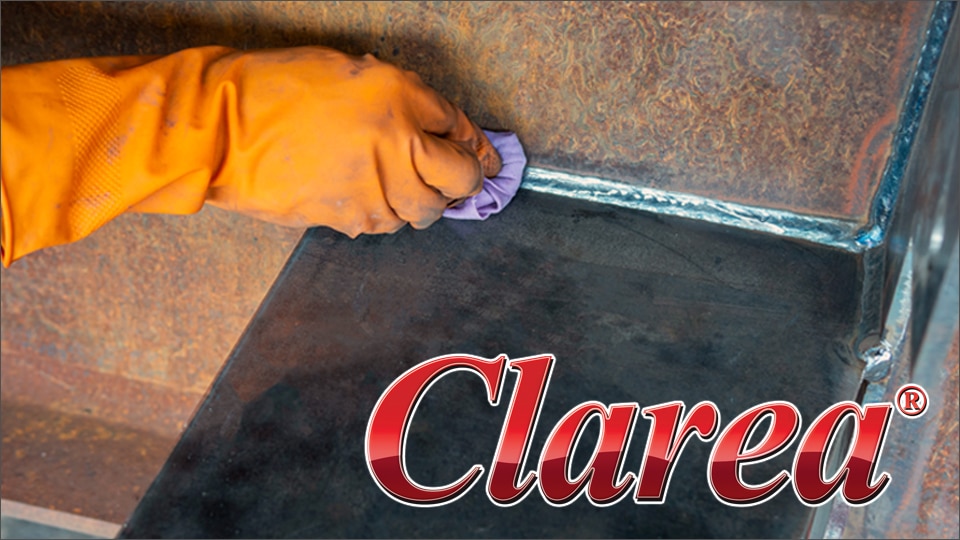
Hand or bath cleaning solvents are used in many industries to remove dirt, oil, grease, or other contaminants from machined and fabricated metal, plastic and composite surfaces. Due considerationmust be given to the effects on users and the environment. Cleaning solvents must be highly refined and leave no residues on drying. They have to be very effective in removal of oils and soils without causing damage or corrosion of the parts or components being cleaned.
Pre-used parts or assemblies from the transportation, aerospace or manufacturing equipment sectors are often very heavily contaminated when removed from service but must be free of all contaminants before handling to disassemble prior to refurbishing and rebuilding. Much of this work will be manual and the considerations for the safety of operators is paramount.
Growing concerns regarding environmental and health hazards of the commonly used chlorinated solvents for industrial degreasing and cleaning has led to the formulation of the Clarea® range of industrial cleaning solvents by EnviroTech Europe.
An environmentally safe range of hand and bath solvent cleaners
Clarea® industrial solvent cleaners are compatible with all metals, composites and most plastics used to remove dirt, oil, grease, or other contaminants from surfaces without causing harm or leavingresidue. They are used as immersion cleaners for component cleaning in manufacturing andengineering industries and as wipe cleaners for large surface areas prior to painting or powder coating. Clarea® cleaning solvents are aliphatic hydrocarbon-based degreasing solvents with specified flash points. They are non-carcinogenic, low odour, fast drying and cause no ozone depletion. They leave minimal residues on drying surfaces and contain no halogens such as chlorine or fluorine.
Clarea HC40 is a degreasing solvent with a flash point of 40°C. It is suitable for brush and hand wiping processes.
Clarea HC62 is a degreasing solvent with a flash point over 60°C. It is suitable for spray or immersion cleaning, or hand wipe applications when used externally.
Clarea HC96 is a degreasing solvent with a flash point of 96°C. It is suitable for spray or immersion cleaning.
Product Benefits
● Versatile and cost-effective solutions for all your industrial cleaning.
● Minimal odour and low toxicity for operators.
● Multipurpose uses can reduce the inventory of cleaning fluids.
● Flexible uses – evaporation rates suitable for hand wipe, spray, or immersion tank cleaning.
● Contains no chlorine, other halogens or stabilisers.
● Compatible with all metals and composites and most plastics.
● Excellent pre-cleaner for paint or powder coatings.
● Safe, reliable, environmentally friendly cleaning.
Solvent Properties
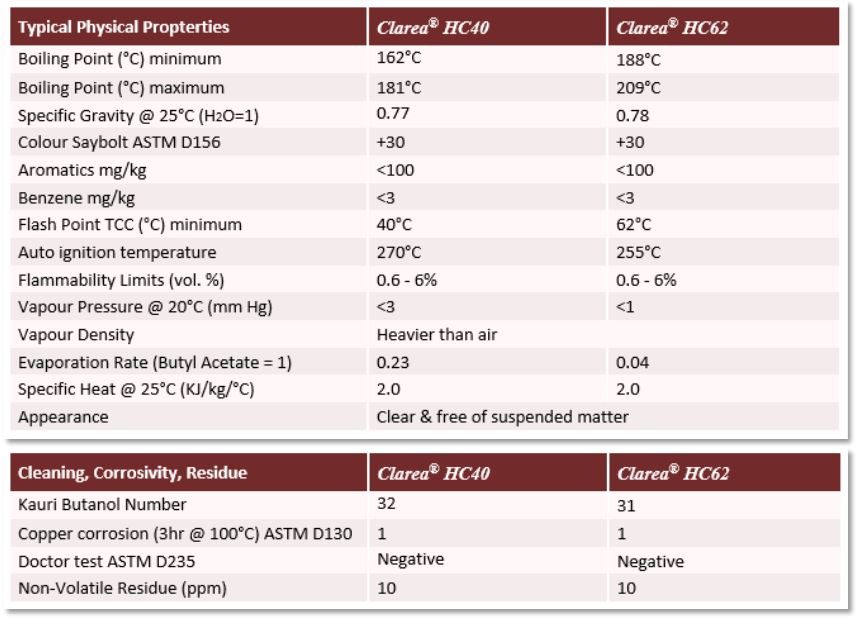
Packaging
Clarea® HC40 and Clarea® HC62 is available in the following container sizes and weights:
205 litre drums, 25 litre cans, 5 litre cans. Clarea® HC96 is available in 15kg cans and 165kg drums.
We can provide you with a Material Safety Data Sheets, independent laboratory reports, product samples and technical assistance.
For more information or advice please telephone us on +44 (0) 20 8281 6370 or use our contact form.
All products are supplied and supported by EnviroTech Europe Ltd. Manufactured in the United Kingdom and available on short delivery times through our dedicated team of distributors worldwide.
Share this page:
Related Posts
Latest News
SuperCORR A protection for USB contacts
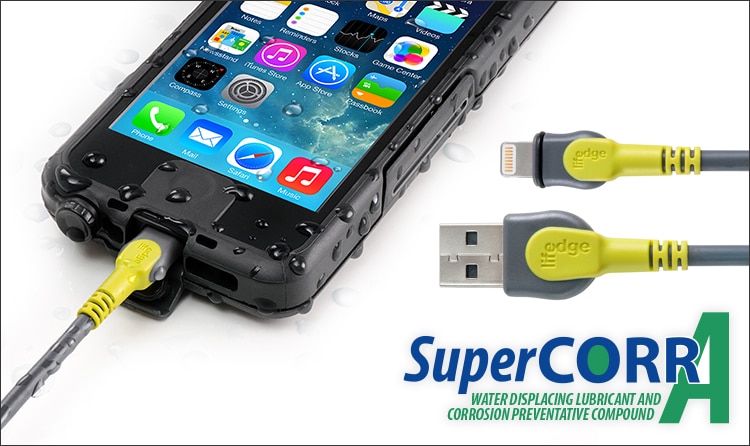
SuperCORR A protects and lubricates contacts on the new Charge / Sync Cable from Lifedge
SuperCORR A lubricant and protective coating widely used by the military, electronics and aerospace industries for critical applications is used to protect contacts on the Lifedge lightning connector to USB cable to offer the protection needed in extreme conditions.
SuperCORR A deposits a dry protective film with excellent corrosion protection and lubricant properties plus the added advantage of a hydrophobic surface rejecting water that ensures the easiest and best connection for the very close spaced connectors.
Lifedge is the world’s first 100% waterproof, rugged Lightning to USB cable for charging and mobile connections whatever the weather or conditions. Developed for use in all outdoor activities including sailing, hiking, military, naval, surveying or other challenging uses. With an ultra-durable outer coating that will never fray and double-moulded, super-tough plugs, charging, downloading and data transfer is improved even in the most extreme and difficult conditions.
During the design of this new cable an extensive test programme, by Scanstrut, manufacturer of the Lifedge cable, was carried out to ensure the contacts were protected from corrosion in the salty and hostile environments in which the Lifedge connectors are used.
SuperCORR A dry lubricant widely used for critical applications in military, electronics and avionics industries proved to offer the protection needed. SuperCORR A prevents or delays corrosion and possible failures.
Testing by a major electronics connector manufacturer recognized that SuperCORR A is a lubricant formulated with corrosion preventive compounds, and as is the case with all “lubricants” will be worn off over time. SuperCORR A was tested to see what the “life” of the lubricant was in a “rub test”. The typical test is 20,000 cycles, i.e. unplug/plug in is one cycle. The test results demonstrated that after 20,000 cycles there were no failures. It was decided to take it one more step and run the same tests for 200,000 cycles. The results again showed no indications of galling or scoring on the USB connectors which looked and performed as good as new.
The extensive testing during the design of the Lifedge connectors validated the original tests and confirmed SuperCORR A will ensure the customer has the most reliable and easy to use connector, in often demanding circumstances. The robust Lightning and USB metal connectors are coated with SuperCORR A patented anticorrosion treatment for complete protection against the elements, whilst an integrated O-ring ensures IP66 waterproofing when charging with the Lifedge iPhone case. The cable is also compatible with protective cases from other leading manufacturers. Officially approved by Apple for use with iPhone, iPad and iPods SuperCORR A helps to bring new freedom and reliability with the Lifedge Ultimate Charge/ Sync Cable.
SuperCORR A is available as an aerosol spray and in bulk containers for brush and dip coating.
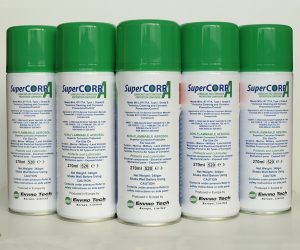
We can provide you with a Material Safety Data Sheets, independent laboratory reports, product samples and technical assistance.
For more information or advice please telephone us on +44 (0) 20 8281 6370 or use our contact form.
All products are supplied and supported by EnviroTech Europe Ltd. Manufactured in the United Kingdom and available on short delivery times through our dedicated team of distributors worldwide.
Share this page:
SuperCORR A Corrosion Protection Spray
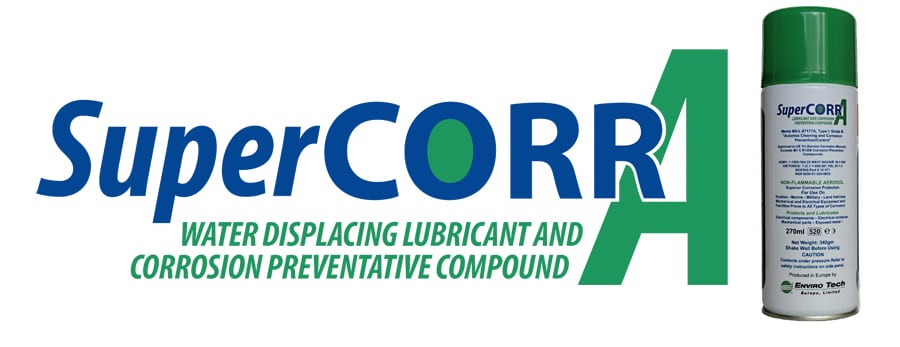
Dry lubricant and corrosion protection spray reduces production downtime on industrial automation systems
Improving manufacturing productivity needs increasing numbers of robots, handling and positioning systems and conveyors which in factory environments need both scheduled and emergency maintenance plans to ensure continuous reliability. Failure of any part of the system will result in downtime and seriously disrupt production.
SuperCORR A from EnviroTech Europe is an innovative thin film dry lubricant spray with corrosion protective properties which does not attract dust or dirt, is stable and coats surfaces with an ultra-thin self healing, lubricant film unaffected by water or solvents and resistant to harsh corrosive atmospheres and high temperatures.
A recent case affected some clients of specialist cleaning equipment manufacturer C&C Hydrosonics a division of U.S giant Crest Ultrasonics to solve a problem occurring on x-y axis linear tracks on the Transystem automatic handling system fitted to enclosed multi tank cleaning systems both aqueous and solvent based.
Transystem automatic handling systems are programmable to automatically process baskets or jigs through liquid immersion cleaning cycles, transferring between the tanks, lowering and raising work between the tanks of cleaning liquids. The motorised carriages use nylon wheels running on case hardened mild steel tracks which can corrode during immersion and in the harsh humid atmospheres within the machine canopies.
Corrosion prevents smooth running with wheels seizing and binding on the tracks. Vibration can then cause components to be shaken from jigs or in extreme cases the carriage will stall requiring intervention by maintenance engineers to physically remove surface corrosion and re-lubricate tracks with oil. This is only a temporary measure as the oil is quickly removed by the solvents or water-based cleaning solutions with corrosion reoccurring in a short time.
Extensive trials over a six-month period with both water and solvent based systems demonstrated that SuperCORR A offered a simple solution to the problem with no corrosion of tracks or seizures during the trial period. Previously seizures needing attention occurred every few weeks now an aerosol spray of SuperCORR A is used only during normal service visits and is used as the routine lubricant during manufacture of the handling system.
Lee Casey, Managing Director of C&C Hydrosonics is delighted with the cost savings on reduced service and maintenance calls using SuperCORR A and that the inconvenience for users of the Transystem equipment has been eliminated. Use of SuperCORR A is recommended on all Crest handling systems worldwide.
Reduce maintenance costs and protect automation equipment with SuperCORR A, now available from EnviroTech Europe Ltd and distributors worldwide.
We can provide you with a Material Safety Data Sheets, independent laboratory reports, product samples and technical assistance.
For more information or advice please telephone us on +44 (0) 20 8281 6370 or use our contact form.
All products are supplied and supported by EnviroTech Europe Ltd. Manufactured in the United Kingdom and available on short delivery times through our dedicated team of distributors worldwide.
Share this page:
Related Posts
Aquus CL-One Concentrated Water Based Cleaner
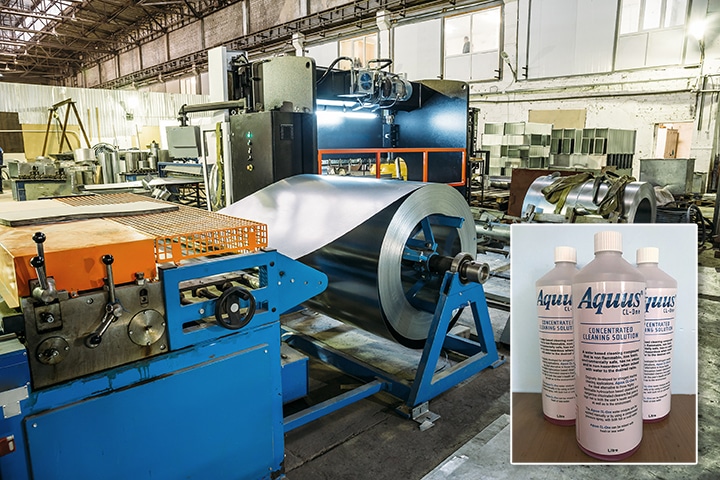
Concentrated water based cleaner for all applications in manufacturing, engineering and general maintenance.
Aquus CL-One cleaner is a new formulation designed to deal with all cleaning applications encountered in manufacturing and engineering. It reduces time and costs by removing the need for multiple cleaning products usually needed to deal with the challenges presented by the wide range of soils, oils and other contaminants which need to be removed. Safe for the environment and users, contains no solvents and is biodegradable within 30 days. Typical applications in industry are discussed below but many more will be experienced in day-to-day operations. With only one product for all cleaning applications incorrect selection or dangerous uses can be avoided.
Concentrated Aquus CL-One chemistry is activated by water, varying concentration levels allows the most economical solution to be chosen for specific applications from parts cleaning to surface preparations for finishing or heavier soiling on process machines all from one product. Some of the hundreds of applications are discussed below.
PARTS AND COMPONENT CLEANING
Ideally suited for cleaning protective coatings, grease and soils from new or used parts. Aquus CL-One can be used in parts washing equipment or dipping tanks without modifications and leaves no residue after drying. Oil and grease separate from the water and coalesces on the surface of the cleaning solution which can then be skimmed off for recovery and recycling. Precipitated solids free of hydrocarbons can be removed by settlement or in filtration systems. The cleaning solution can be reused continuously within its chemical parameters for efficient and economical use.
GENERAL CLEANING
Aquus CL-One is remarkably efficient removing oils, greases, and accompanying dirt from most surfaces. It can be applied by wiping surfaces, mopping or in rotary floor cleaning machines, low or high-pressure spray. Aquus CL-One is also an effective cleaner in industrial kitchens removing grease and baked on deposits on internal surfaces of ovens and trays. For maintenance of machines, engines etc oil and grease is easily removed pre and post-assembly making inspection and repair easier, quicker and cheaper by returning equipment to use.
PREPARATION FOR PAINTING OR POWDER COATING
Aquus CL-One is an excellent choice for cleaning mild steel and ferrous metal parts which are not painted immediately. Process oils and grease on the parts protect the surfaces from changes in humidity but once removed flash rusting can occur while drying. Aquus CL-One prevents this leaving an invisible barrier on the metal surfaces providing extended corrosion protection during storage, fabrication or assembly before finishing. The barrier film can be painted over without additional rinsing and without affecting adhesion of paint or powder coatings. Various cleaning systems can be used, including hand wiping, dip tanks and pressure washing.
Our applications experts and samples of the product are available by completing the contact form at our website. For more information please visit:
Share this page:
Related Posts
Corrosion control problems
Corrosion control is a serious problem for industry and governments worldwide.
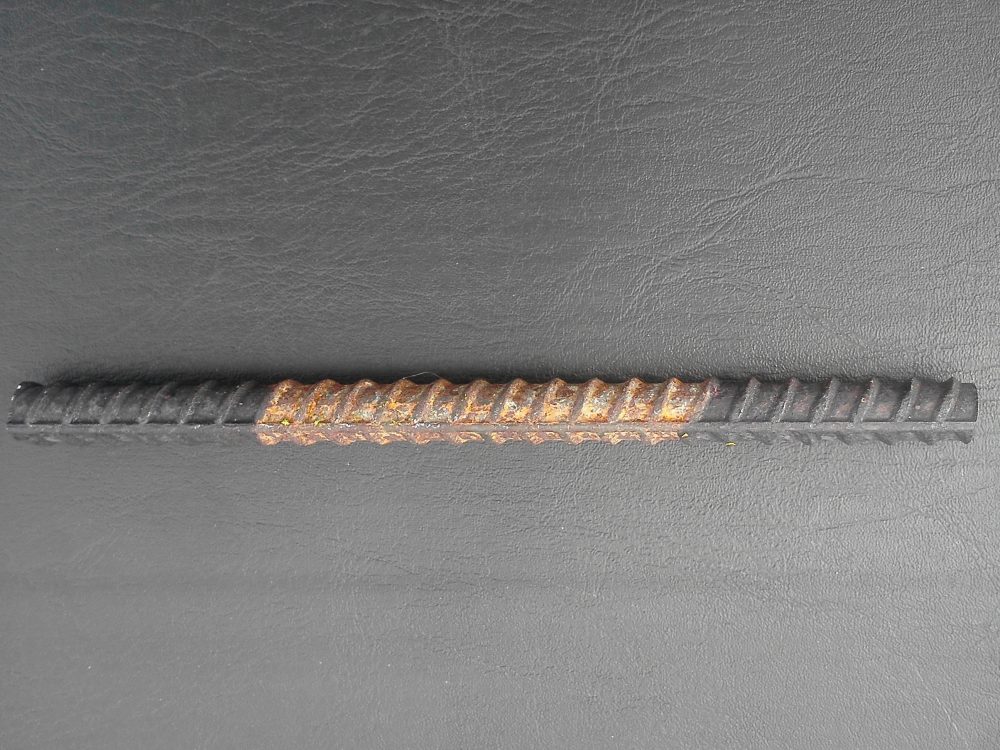
Most people associate corrosion with rust, which only happens in things made of ferrous metals such as steel girders, ships, iron pipes, steel reinforcement rods, and steel tanks and is the reason metals deteriorate and fail.
Ferrous and non-ferrous metals corrode on contact with both fresh and salt water as well as water vapor. They will also corrode when they come in contact with chemicals, liquid acids as well as acidic vapors, salts and bases, and bacteria.
Read our article “Corrosion Control Solutions – A Solution To A Costly Problem” for more information about the enormity of the costs involved in failing to prevent corrosion.
We can provide you with a Material Safety Data Sheets, independent laboratory reports, product samples and technical assistance.
For more information or advice please telephone us on +44 (0) 20 8281 6370 or use our contact form.
All products are supplied and supported by EnviroTech Europe Ltd. Manufactured in the United Kingdom and available on short delivery times through our dedicated team of distributors worldwide.
Share this page:
Replacements for nPB
Envirotech Europe introduce low cost “drop in” replacements for nPB (n-propyl bromide) vapour degreasing solvents.
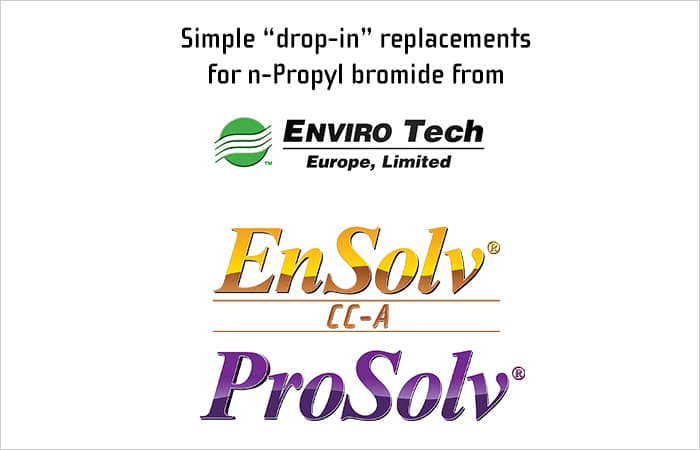
Bad news for your business. Coronavirus, Brexit, redundancies, social distancing reduced cash flow.
If that’s not enough and you are using nPB solvent that’s another problem to worry about as its use for vapour degreasing has been banned by the EU since July. Don’t panic it’s not too late to change and comply, as we have “drop in” replacements for nPB which are guaranteed to give the same results at no increase in your costs of usage. It is late but we can give you the information to easily make the change in a day without fuss.
You have questions – of course:
How can it be so simple?
The EnSolv range of stabilised nPB based vapour degreasing solvents has been the market leader in this field worldwide for many years. EnviroTech Europe, the manufacturers, know this product inside out with hundreds of satisfied users. We have been fighting the EU authorities for 20 years regarding classification, but with limited resources and the corporate giants with money to lose as EnSolv gained more and more of the market. Money talks so the Commission ignored the evidence and banned nPB for use as a vapour degreasing solvent with the sunset date in July 2020. If you are interested in the history, it is all explained in detail on our website.
With our extensive knowledge of user needs EnviroTech Europe, during the intervening years, have developed new compliant solvent formulations which are simple “drop-in” replacements.
No new equipment needed, guaranteed results and no extra costs to worry about.
We can’t guarantee that more changes will not happen in the future, but you will then have time to evaluate whether the new generation of wonder products which reduce global warming a smidgeon is worth the enormously increased costs.
Talk to us about whether EnSolv CC-A or ProSolv will be the best choice for your application. Advice, literature, changeover instructions are all available to make the change quickly, easily and at no extra cost of usage.
For more information about replacing nPB please visit:
www.vapour-degreasing.com/npb-replacement
We can provide you with a Material Safety Data Sheets, independent laboratory reports, product samples and technical assistance.
For more information or advice please telephone us on +44 (0) 20 8281 6370 or use our contact form.
All products are supplied and supported by EnviroTech Europe Ltd. Manufactured in the United Kingdom and available on short delivery times through our dedicated team of distributors worldwide.
Share this page:
Related Posts
Corrosion Protection Spray – SuperCORR A
SuperCORR A corrosion protection spray protects and revitalises production machines during Coronavirus lockdowns.
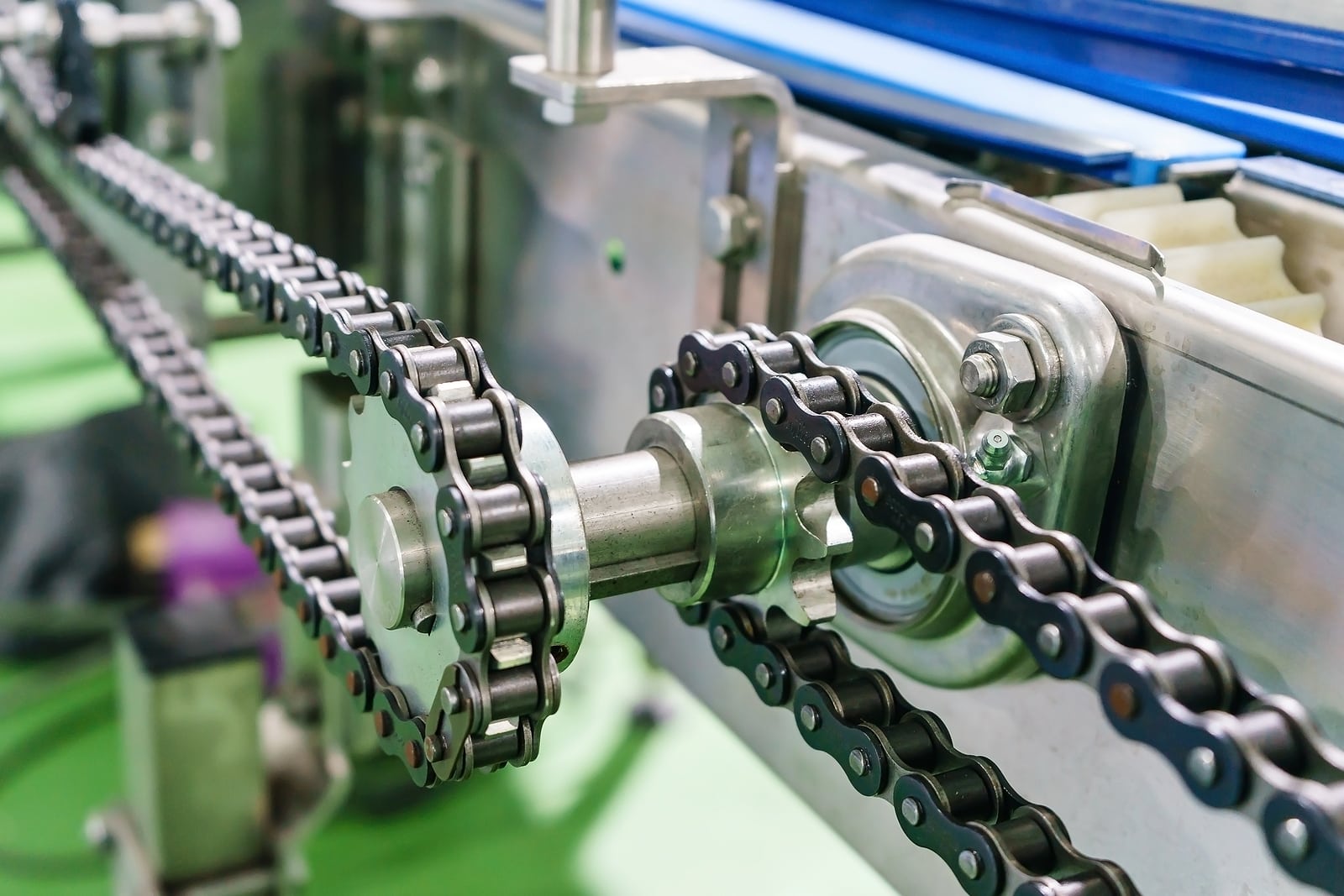
Spraying a coating when shutting down machines, drives, conveyor chains and in control cabinets will prevent or displace condensation on exposed surfaces protecting against condensation. A further spray on reopening and restart displaces any surface moisture which may have accumulated and relubricates moving components.
SuperCORR A is a proprietary formulation containing no organic constituents. A combination of long lasting synthetic anticorrosion inhibitors and lubricants that protects metal components against moisture. This unique, water displacing lubricant is non-flammable and environment friendly.
Unexcelled in preventing corrosion and contamination on all surfaces in mechanical close tolerance slow moving components or electrical and electronic equipment used in humid conditions. Can be used on any metal surfaces to prevent flash rusting, microbial and other forms of corrosion.
SuperCORR A forms a super thin, hydrophobic, non-flammable lubricant film with anti-corrosion properties approximately 7 microns (0.007mm) in thickness and is compliant with U.S. EPA regulations, the European Union RoHS Directives
Conforms to MIL-DTL-87177B (Revised MIL-L-87177A) specifications.
For more information please visit www.corrosion-protect.com/supercorr-a To discuss the use of SuperCORR A to solve your corrosion protection problems please use the website contact form or phone us, we look forward to hearing from you.
We can provide you with a Material Safety Data Sheets, independent laboratory reports, product samples and technical assistance.
For more information or advice please telephone us on +44 (0) 20 8281 6370 or use our contact form.
All products are supplied and supported by EnviroTech Europe Ltd. Manufactured in the United Kingdom and available on short delivery times through our dedicated team of distributors worldwide.
Share this page:
Related Posts
Improve connector maintenance on portable gas generators
Why using SuperCORR A for connector maintenance on portable gas generators improves electrical supplies in extreme conditions.
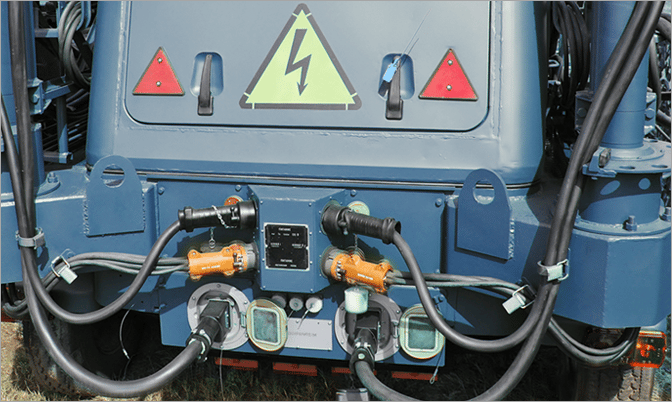
Portable generators maintain aircraft services at standings are connected and disconnected many times a day in extreme weather conditions.
These applications and locations test connector seals allowing dust or water to infiltrate. This with the flexing of the connecting cables allows sufficient movement between the metal surfaces of the connecting pins to produce fretting corrosion which reduces, interrupts or produces failures in electrical supply. Regular maintenance of electrical connectors and control systems is vital to be certain of uninterrupted supply.
SuperCORR A is an aerosol lubricant containing corrosion preventive compounds, which, as is the case with all lubricants, can be worn off over time.
A leading manufacturer of connectors tested SuperCORR A to see what the “life” of the lubricant was in a “rub test”. The typical test is 20,000 cycles, i.e. unplug, plug in is one cycle. The test results demonstrated that after 20,000 cycles there were no failures. It was decided to take it one more step and run the same tests for 200,000 cycles. The results again showed no indications of galling or scoring on the connectors at all. The connector looked and tested as good as new. This test was run under clean conditions in a laboratory but demonstrates the effectiveness of the protective lubricant in SuperCORR A.
As it meets Mil- MIL-DTL-87177B (Revised MIL-L-87177A) specifications SuperCORR A is used by the U.S. Air Force to protect the intricate workings of the F-16 Fighter Jet and by the U.S. Navy on the P 3 Orion electronic surveillance aircraft. Commercial aviation aircraft manufacturers recommend it for electrical and close metal mechanical application, especially where flights are in salt fog or high humidity.
Containing extremely long-lasting, proprietary anti-corrosive inhibitors SuperCORR Aprovides a superior lubrication coefficient and protects components against moisture, wear, general and fretting corrosion, surface static electricity, corona, and other electro migration problems. The super thin non-flammable lubricant film is only 7 microns (0.007 mm) thick and is formulated without sulphates, chlorides or halogens to meet the RoHS directive. It is unexcelled in preventing deterioration and contamination on all surfaces of electronic equipment.
Very fast drying environmentally acceptable solvents are used as carriers and propellants which will not affect most plastics, substrates, metals or other materials used in connector manufacture.
The aerosols are supplied with probes allowing access to pins and connector tubes where the low surface tension repels water, dirt dust and metal particles from blind holes and surfaces to produce thoroughly clean holes before a second application applies the lubricant film. Reconnection to the supply with cleaned sections of the connector ensures reliable operation even in the most testing of environments. This easy maintenance from one can of
SuperCORR A allows this essential task to be carried out in any conditions quickly, easily and securely.
For more information please visit www.corrosion-protect.com/supercorr-a To discuss the use of SuperCORR A to solve your problems please use the website contact form or phone us, we look forward to hearing from you.
We can provide you with a Material Safety Data Sheets, independent laboratory reports, product samples and technical assistance.
For more information or advice please telephone us on +44 (0) 20 8281 6370 or use our contact form.
All products are supplied and supported by EnviroTech Europe Ltd. Manufactured in the United Kingdom and available on short delivery times through our dedicated team of distributors worldwide.
Share this page:
Related Posts
Replace n-Propyl bromide with ProSolv vapour degreasing solvent
High performance vapour degreasing solvent, simple “drop-in” replacement for n-Propyl bromide and trichloroethylene.
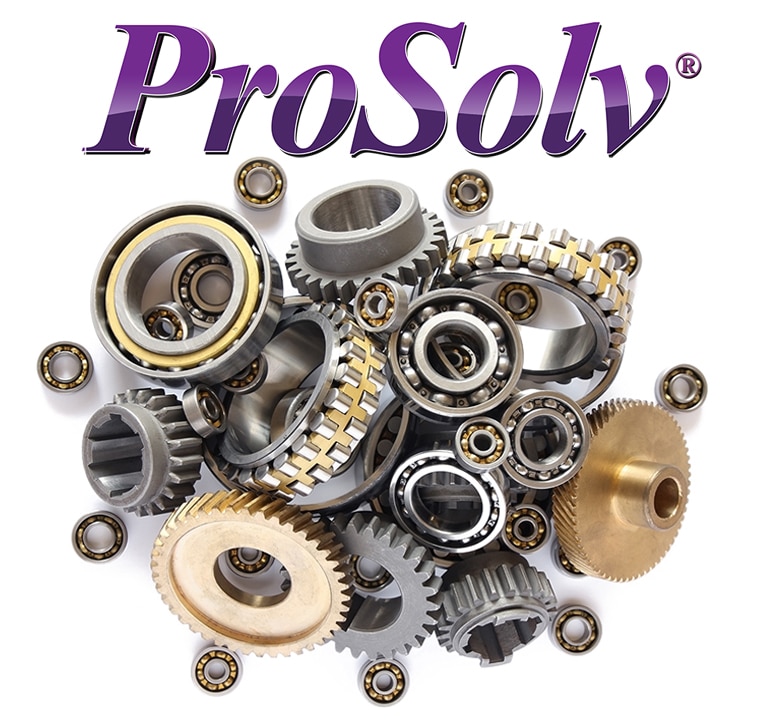
ProSolv® is an alternative chemistry developed by EnviroTech Europe to replace chlorinated solvents. It can be used in most existing vapour degreasing equipment and can be used safely for immersion cleaning using ultrasonics, for which it has been optimised. with a high specific gravity and very low surface tension.
Unlike some other chlorinated and halogenated blends such as trichloroethylene, ProSolv® is an excellent choice to replace flammable solvents such as MEK, Acetone, Isopropyl alcohol (IPA) or hydrocarbons where manual wiping or brush cleaning is the preferred method. It is a non-flammable azeotropic blend which can be used for manual cleaning in suitably ventilated areas and recycled by distillation for reuse through many cycles. It is a very stable mixture with no need for monitoring or the need for additives or stabilisers.
In other applications ProSolv® offers a cost-effective alternative for halogenated solvents in formulations for dip, spray or aerosol applications and as a fast-drying carrier solvent for oil, silicones and other lubricants. Simple to install in any standard machine for vapour and vapour liquid degreasing.
ProSolv® is non-flammable (No Flash Point) with high solvency (KB Value 91) with a very low surface tension and low boiling point making it highly productive and economical in use. A very stable azeotrope in use no additives or testing required. Leaves minimal non-volatile residue.
Importantly the ProSolv® formulation is kind to the environment as it contains no hazardous air pollutants and is safe for users. It has zero ozone depletion (ODP) with very low global warming potential (GWP). ProSolv® is compatible with all metals.
Manufactured in UK with excellent customer service, technical support and training from qualified distributors throughout Europe.
We can provide you with a Material Safety Data Sheets, independent laboratory reports, product samples and technical assistance.
For more information or advice please telephone us on +44 (0) 20 8281 6370 or use our contact form.
All products are supplied and supported by EnviroTech Europe Ltd. Manufactured in the United Kingdom and available on short delivery times through our dedicated team of distributors worldwide.
Share this page:
Related Posts