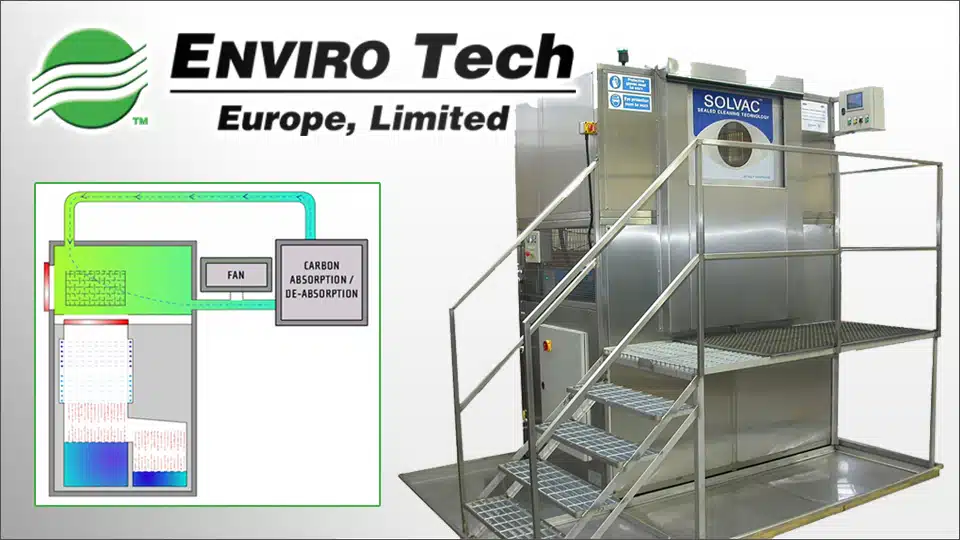
Solvent Degreasing and Metal Cleaning –
Future proof Vapour Degreasing from EnviroTech Europe
Innovation driven by legislation
Vapour degreasing, with or with-out ultrasonics, is the oldest, simplest and most effective solvent degreasing and metal cleaning process used today. It has, until recently, been subject to little change since it was first invented in the early part of the last century. In the UK, Europe, United States and other advanced industrialized economies increasingly stringent legislation to control emissions of VOCs, Global Warming Compounds, Ozone Depleting Compounds, and those compounds associated with human health concerns has led to new formulations for precision cleaning solvents.
Cleaning systems have had to change too. With increased legislation concerning the regulation of health and environmental safety, uses of solvents have been targeted and alternatives are encouraged by the relevant authorities and law makers, often without serious consideration of unintended consequences. For example, water-based cleaning is the obvious alternative but this has many disadvantages compared to vapour degreasing as although the machines are simple and relatively cheap the processes require multiple tanks for immersion or spray processing or long programmed cycles in batch machines for cleaning, rinsing and drying. Water based processes are slow, energy intensive and occupy more floor space than vapour degreasing equivalent where only one tank with small footprint is needed delivering shorter process times and most importantly using minimal energy. Then there is the disposal concern as the used water cannot just be disposed of by pouring it down a drain.
The ideal cleaning process would be vapour degreasing and cleaning with water, but due to the physical characteristics of the vapour/steam and the inability to carry surfactants to remove the oil, grease and soils and the difficulty of rinsing and especially drying this will only ever be a dream.
Halogenated hydrocarbons are the solvents of choice for vapour degreasing and cleaning. The process is essentially simple. A tank with a sump to contain the solvent, heaters at the base and condensation coils around the top section to control the height of the vapour is all that is needed. When heated in the sump halogenated solvents produce, in most cases, a saturated vapour between 3 and 4 times heavier than air at a temperature greater than the ambient temperature of the parts to be cleaned. This allows the solvent vapour to condense on the surface of the parts. The condensate dissolves the contaminants such as oil, greases, flux, and soils returning the used solvent into the sump of the machine for recycling into vapour which continuously condenses onto the parts until they have achieved vapour temperature when, with no further condensation, the process is complete. Parts removed from the cleaning machines are very clean, warm and dry.
The most common halogenated solvents, in use for commercial purposes, are non-flammable so present no risk in this process. Perchloroethylene, used mainly for dry cleaning, methylene chloride previously used widely in paint strippers, 1,1,1- trichloroethane and trichloroethylene used for vapour degreasing were the original materials used based on chlorine chemistry. However continuing concern about the environmental impact and danger to operators by exposure to chlorine-based solvents, especially trichloroethylene, has led to a continuing search for safer alternatives, such as ProSolv 5408e, a trans-1,2-Dichloroethylene based solvent mixture that is non-flammable.
As with all legislation for chemical use regulation and restrictions drive development of associated processes and equipment. The most important developments in vapour degreasing cleaning machines to use solvents for vapour degreasing use two different approaches and raise difficult questions as to which is the best most economical and simplest in use.
The single tank hermetically sealed machines favoured by mainly German manufacturers uses a process tank to contain the solvent and a separate storage tank/vapour generator. Baskets with parts to be cleaned are loaded from the top and lowered into the process tank. A lid then closes over the tank and is hermetically sealed. Solvent is pumped into the process tank. Baskets are immersed in the solvent where agitation, ultrasonics or pumped liquid is circulated through the parts. When the immersion process is complete solvent is pumped to the storage tank and vapour fed to the process tank from a vapour generator for rinsing and drying. Condensing coils/panels controlling the vapour height are linked to coils located within the vapour zone which, when the cycle is complete, collapse the vapour. The process tank is emptied. The saturated air/solvent from the process tank is then recycled through carbon absorption units to remove traces of solvent from the air until the concentration is below 2 grams per cubic meter when the lid opens automatically for the basket of parts, clean and dry, to be removed and replaced with a further basket.
Variations within the hermetically sealed tank are possible using sprays of cold or hot condensed solvent, immersion with or without ultrasonics and revolving baskets to cover most of the problems experienced when processing machined and fabricated parts. Continuous external distillation of the contents of the vapour generator is also an option depending on contamination.
The alternative technology is much simpler and cheaper and less time consuming using well trained techniques. This is favoured by UK based manufacturers. The multilevel system shown in the diagram uses a standard vapour degreasing tank design with a sealed loading section above the process tank.
Work baskets are fed to the load section from a hoist or conveyor. The loading door is then pneumatically sealed to hermetically isolate the process. The sealing lid on the process tank is opened and the basket lowered into the cleaning tank which can be simple vapour degreasing with vapour generator below or an offset generator can be used with the lower section being filled with clean solvent for immersion cleaning with or without ultrasonics or power sprays. Revolving baskets can also be added to improve cleaning in blind or through holes or oil ways in castings and fabrications.
When the process is complete the basket rises to the freeboard area where the condensation coils are located, and parts are allowed to drain and dry. The tank seal opens to allow the basket into the load section while the lid closes again across the process tank. A fan is then activated which produces a negative vacuum in the load area. The loading door is then partially opened to allow a flow of air through the loading section which is exhausted to atmosphere or can be recycled through carbon absorption systems if no external exhaust is preferred. As baskets entering the loading space contain parts drained and dried only very small amounts of solvent are carried in the exhausted air which is monitored to ensure compliance with local legislation. When this is achieved the door opens fully for removal of basket. The loading section can be fitted with top or side sealed doors allowing baskets to flow through on conveyor systems or be loaded from hoists. No solvent enters the work area. Both processes will produce parts cleaned to the highest standards but the choice of which offers the best solution needs a little more consideration.
The single tank process is complicated with the need to move liquids in the machine. It is relatively slow as the carbon adsorption process needs to remove high levels of solvent from the recirculated airstream from the process tank. This is inefficient as adsorption rates for carbon fall rapidly with increasing saturation. Final levels of solvent in the tank when the lid opens will be dragged into the workshop and the area in which the operator is working. Long process cycles reduce throughput.
The simpler multilevel systems where movement of liquids is not required are more efficient and offer much faster process times. Cost of manufacture is also cheaper as no liquid movement is involved. The extracted loading section ensures no leakage of solvent into the work area which offers complete safety for operators and factory staff. The disadvantage of the multilevel machine is the height of the equipment compared to the single tank machine. This will often require the equipment be installed in a pit for easy access.
Both designs of process machines fully comply with the emission regulations of the UK, EU and U.S authorities. Which to choose will depend on many factors which should be discussed with both the equipment and solvent suppliers who have the experience to advise on which offers the best process for the application. Equipment and solvent must work together and it is advisable to ensure that the suppliers work closely together to offer a package with high levels of responsible care and product stewardship to ensure the best and safest installation.
The vapour cleaning process still gives the highest levels of economical cleaning with minimum energy usage, low footprint on the factory floor, safety for the operator, and high production rates with low solvent usage or environmental impact. With the new generation of sealed cleaning machines its future as the process of choice is assured.
Envirotech Europe supplies three distinct products that use this process and we are happy to advise you on the best solution to suit your needs. Please visit our website to find out more about ProSolv 5408e, ProSolv and EnSolv® CC-A.
Image of Solvac hermetically sealed equipment by kind permission of CC Hydrosonics Ltd.
FURTHER INFORMATION
Please visit our website www.envirotech-europe.com for information about other uses and applications for our vapour degreasing and cleaning products.
Visit www.envirotech-europe.com/applications-and-case-studies for information about uses and applications for all EnviroTech Europe products.
For more advice, please telephone us on +44 (0) 20 8281 6370 or use our contact form. All products are supplied and supported by EnviroTech Europe Ltd. Manufactured in the United Kingdom and available on short delivery times through our dedicated team of distributors worldwide.
Share this page: